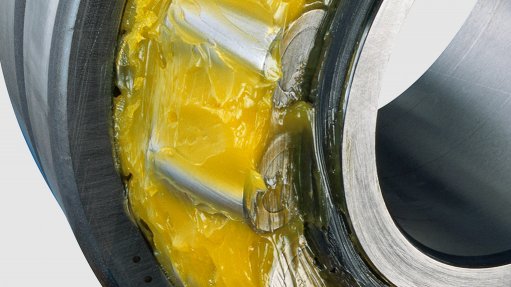
“Lubrication management can make or break asset performance, therefore getting it right will provide a sound foundation for asset reliability,” notes SKF Lubrication solutions and dealer manager, Jan Backer. Citing a food and beverage industry estimation that states ‘15-25% of maintenance budget is lost due to poor lubrication management’, Backer warns that getting it wrong can have expensive consequences.
Ever tightening industry regulations to ensure food safety are placing demands on companies to explore alternate methods to manage lubrication. Companies are also pressured to set targets for environmental responsibility and sustainability, factors both which can be impacted by the way lubrication and re-lubrication is executed. Backer suggests that the food and beverage industry should reconsider lubrication practices and investigate alternative technologies that provide food and operator safety, optimised costs and environmental benefits.
While there are many technologies available in relation to lubricants and lubrication, identification of potential negative impacts on Hazard Analysis and Critical Control Points (HACCP) has led to the emergence of a different approach in managing lubrication proactively. Backer recommends managing lubrication as a strategy instead of as a practice. “Good lubrication practices are widely accepted as fundamental to plant reliability. But it is less about re-lubricating and more about the choices made to achieve the right outcome. It is important to note that not all lubrication practices are effective and costs can be daunting.”
Effective manual lubrication requires knowledge about how much, with what and how often. Re-lubricating exactly the right amount, at the right time, using the correct lubricant is an applied science. The consequences of ineffective lubrication which includes both under- or over-lubrication can be excessive downtime, high spares consumption, food and operator safety risks and ultimately an expensive toll on the maintenance budget. In other words, lubrication actions can often cause as many problems as they solve i.e.:
- Frequent re-lubrication implies grease and labour costs, re-lubrication to purge bearing positions
- Contamination risk: Over-lubrication can compromise food safety
- Operator safety: Re-lubricating in hazardous working areas with difficult access; leaking seals can cause slips and costs related to absenteeism due to injuries are high
- Resources & skills: challenge of skill level in the industry to perform the correct re-lubrication and retaining that knowledge
It is common practice to re-lubricate bearings after each wash-down, a process during which excess grease is discharged (purged) past the bearing seals. Alongside compromising food and people safety as well as asset reliability, the next wash down cycle washes the grease away and into the plant’s waste water which has a negative environmental impact.
There are different ways to meet these challenges and SKF offers a wide spectrum of product and service-based solutions. “We do more than traditional lubrication management which only looks at lubricants and how to apply them. We bring technologies that eliminate the need to re-lubricate, adding value from a food safety, cost, reliability and environmental perspective. What makes the difference is our deep knowledge of rotating equipment, industry experience and commitment to reduce the customer’s cost of ownership.”
Among the dedicated technologies available to support management of the lubrication of food and beverage processing machinery, re-lubrication-free bearings, advanced sealing systems, automating lubrication solutions and customized training programs available from SKF, have emerged as potential solutions that can mitigate risk of food and operator safety, also avoiding excess lubricants being washed into the waste water stream or disposing of grease cleaning wipes.
“We have always done it this way,” can be seven very expensive words in business. Challenge the way things have always been done. SKF recommends a Technical Assessment of the production process to provide a structure to readily identify potential issues, risks, opportunities and benefits in moving from current approaches. Identification of potential negative impacts on HACCP can lead to areas for improvement where SKF offers a range of technology and service offerings dedicated to helping with lubrication management. These cover for example:
• Re-lubrication-free bearing technologies
• High efficiency seals that keep lubricants in and contaminants out
• Lubrication management: SKF assists with review, optimised lubrication strategies and lubrication routines in order to:
o Apply the right amount of lubricant at the right intervals manually or through automatic systems
o Ensure the use of the right tools following the correct methods
o Set up an appropriate training program for maintenance technicians and operators
• SKF can also provide a smart way to detect poor lubrication conditions by analyzing vibration data through ‘vibration parameters’.
SKF is a leading global supplier of bearings, seals, mechatronics, lubrication systems, and services which include technical support, maintenance and reliability services, engineering consulting and training. SKF is represented in more than 130 countries and has around 17,000 distributor locations worldwide. Annual sales in 2015 were SEK 75 997 million and the number of employees was 46 635. www.skf.com