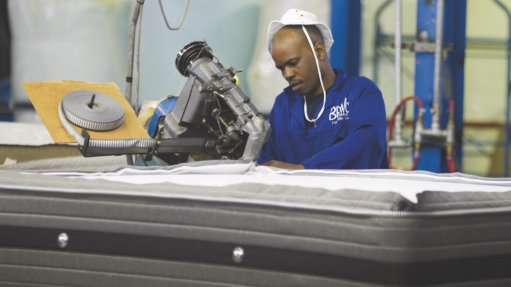
LOW-TECH APPROACH
The Sleep Factory relies on a highly-skilled workforce, capable of easily switching between the manufacture of many different types of sleep products
Photo by: Duane Daws
Langlaagte-based sleep products manufacturer Bravo Group’s Sleep Factory attributes its lion’s share of the domestic premium sleep products market to the use of low technology processes and low levels of automation, instead relying on labour-intensive methods and a refined production line.
The Sleep Factory is the sleep products division of furniture and bed brands manufacturer Bravo Group, which consists of nine factories, all of which are in Southern Africa, with the bulk in South Africa. Six of these factories handle sleep products, while three manufacture lounge products.
Bravo Group has more than 120 years of heritage in South Africa, having set up one of the first mattress factories in Johannesburg in 1895.
In terms of representation in the high-end premium sleep-products market, Bravo Group claims to hold the largest market share, while overall representation in the general sleep products market is about 20%.
Production from the Sleep Factory is driven purely on an order-by-order basis, resulting in short lead times and a significantly low stockholding of raw materials, as well as a very low finished-product holding, as completed products are packed and shipped within hours of having been manufactured.
The Sleep Factory also produces a variety of products under many brand names, including well-known brands in the South African and international markets, such as Sealy, Edblo, Slumberland, King Koil and Stearns & Fosters.
Bravo Group COO Malcolm McDonald tells Engineering News that these brands require different specifications in terms of manufacturing and assembling of line items. Thus, they require skilled technicians to be flexible, adaptable and capable of producing a vast range of products in line with specified quality and standards associated with the many brands offered by the Sleep Factory.
To meet the production requirements of a dynamic order book, which can change at a moment’s notice, Bravo Group relies on an artisanal workforce of 3 500 nationwide.
The Sleep Factory also runs extensive and intensive upskilling programmes, which take place during times of low production requirements, through which artisans are certified. The programmes are presented for about six to eight months of the year.
Bravo Group Sleep Factory GM Anwar Ismail says, through the plant’s lean technology initiative, jobs have been safeguarded and cost savings have been achieved. Further, importing large machinery from overseas adds “unfavourable exchange rates” to costs, which the company has avoided by relying instead on the skills of its workforce.
Of the four sleep products factories in Africa, two are in Johannesburg (one for mattresses and the other for bed bases), one in Durban and one in Cape Town, with two satellite factories in Zimbabwe and Namibia.
Plans are afoot to open an assembly plant in Tanzania before the end of the year.
The Tanzania factory is part of Bravo Group’s vision to expand into the rest of Africa, with East Africa showing significant potential for growth into the sleep-products market.
McDonald says, currently, about 15% of local manufacturing is exported, mainly to the Southern Africa region.