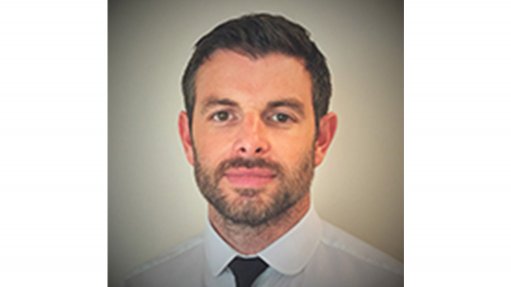
To promote the Lantek Factory concept to sheet metal and structural steel companies in the UK, Lantek has appointed Adam Ball as Sales Manager for the company’s ERP products. More companies are realising that they can gain some very significant efficiency benefits from integrating all their manufacturing systems allowing them to measure performance, in real time, of the key aspects of their business.
Adam Ball says, “I have been involved in supporting and supplying software for the sheet metal industry for a considerable time and there is a clear move towards automation to optimise productivity. Integration of software systems is part of the automation process, enabling users to have an accurate picture of all areas of their business including costs, manufacturing status and customer relationships.”
The Lantek Factory concept is achieved through the integration of Lantek Workshop and Lantek Integra products with the Lantek Expert and Lantek Flex3d CAD/CAM products which handle CAD data, unfold parts, create nests and generate CNC code for the cutting process.
Starting with a customer enquiry, CRM software makes available the complete history of a customer’s orders. Quotation software then makes it very quick and easy to generate an accurate cost to include material, and all the manufacturing operations such as cutting, bending, painting and assembly. At the same time the production schedule can be interrogated to make sure that material is available and that there is sufficient production capacity to deliver parts on time.
Once the order is placed, delivery dates, manufacturing stages and material requirements are all specified and scheduled. These are then synchronised with the other work going through the factory, enabling engineers to create dynamic nests of parts for each material type where appropriate, manage remnant material and prepare parts for cutting while keeping to the delivery dates.
For coordinated manufacture, material is delivered to the machine on time and the operator has setup information available where this is necessary. As production progresses, feedback can be recorded through shop floor terminals, giving real time information on the status of manufacture for managers.
At every stage priorities can be altered where there is an urgent need for particular parts. Managers can see what impact any change will have on the overall performance of the factory. With mobile working commonplace, access via the internet makes it possible for them to provide an exceptional level of service to their customers through having accurate and up to date information at their fingertips, wherever they are.
Throughout the system traceability is secured ensuring the most stringent quality requirements are complied with, while links to accounting systems ensure all administrative tasks are completed accurately and quickly. At every stage, material costs and process times are accurately recorded ensuring the profitability of every part, while an overview of performance enables managers to evaluate future investment plans based on facts.