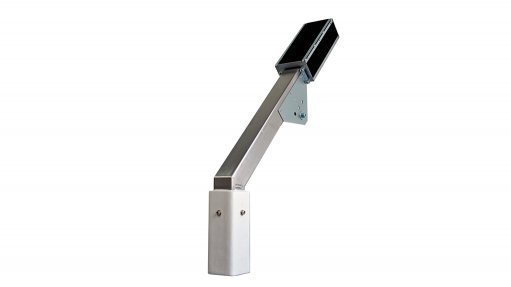
Company Announcement - The University of Stuttgart and IAS GmbH have developed an innovative powerful cooling system for sensor systems in high-temperature areas – applications in the metal processing industry up to 800°C. A cooled sensor system for high-temperature areas up to 800°C – this is the result of a current collaborative research and development project. An innovative Swabian company together with the Institute of Nuclear Technology and Energy Systems at the University of Stuttgart have designed a passive cooling system that facilitates the use of off-the-shelf inductive sensors in high- temperature areas. The main application for this technology is in process optimization for pyrometallurgy in the metal processing industry.
The market for passively cooled inductive sensor systems is large; however, mainstream sensor manufacturers up to now have not served it. „This is due to a one-sided approach and lack of willingness to think outside of the box“, says Steven Hartmann, CEO of IAS GmbH. Mr. Hartmann has therefore dedicated the last three years together with IKE to this special theme. His objective: The development of a passive cooling system for off-the-shelf inductive sensors which can be easily adapted to customer specific applications and is suitable for reliable continuous operation in a „heavy duty environment“.
High-Tech for optimization of metal producing high-temperature processes in pyrometallurgy: The new technology is appreciated for monitoring levels of molten metals in ovens, casting channels, and casting-dies, as well as for controlling the position of hot semi-finished metal products. The non-contact reliable detection of the melting bath level is now feasible thanks to the new high-temperature sensors. Casting processes can thus be optimized through improvement of automation. As well as higher quality and increased numbers of units produced, increased energy efficiency is also achieved.
Innovation lead with the best future prospects
The inductive sensor and high performance cooling are mounted together in a robust housing. The device operates durably, reliably, and requires low maintenance because there is not any contact with the molten metal. Various existing interfaces enable the device to be easily integrated in the different systems produced by market leading control technology manufacturers. Hartmann: „The product is a real alternative to vulnerable contact electrodes.“ Whether for tin or zinc, magnesium or aluminium: The non-contact eddy current detection of various molten metals is now viable.
High-Tech in pyrometallurgy
„With our cooling system, existing sensor technologies and future new inventions can be implemented in the high-temperature area“, explains Mr. Hartmann.
The cooling system is simply constructed and therefore reliable, low maintenance, and cost-efficient.
Heat dissipation is achieved via energy transport using heat pipes directly on the cooled sensor. The heat is transported to the heat sink located on the opposite side at the back end of the housing. From here, the heat is dissipated to the environment.
The company IAS GmbH already have functioning prototypes that can reliably operate in an environment with a temperature of 800 °C. Hartmann: „The series production of the system can be rapidly implemented following evaluation of several planned test systems in industrial environments.“ The cooling system has already been registered as patent. The project is supported by the Federal Ministry for Economic Affairs and Energy within the framework of the Central Innovation Programme for SMEs.