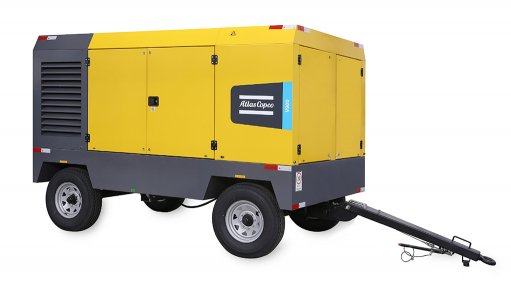
Atlas Copco's DrillAir V900 mobile compressor
A high-pressure compressor that can drill the maximum number of metres a day at the minimum cost a metre, helps ensure business sustainability – and Atlas Copco says that its high-pressure DrillAir compressor range meets this objective.
The company’s power technique business line manager: portable products David Stanford says that the Atlas Copco DrillAir Y35 can drill 500 m a day, which translates to completing two 4.5” geothermal wells in a single drilling day.
A DrillAir compressor uses a combination of pressure and flow to achieve maximum air flow at any pressure setting. The machines are designed to be rugged and flexible, to offer a compressed air solution for a range of high capacity drilling applications. A primary objective is to save time spent and fuel, while increasing drilling performance. “This perfect harmony between pressure and flow puts end-users in full control of these parameters, while saving fuel,” notes Stanford.
Drilling efficiency is enhanced by using the right compressor to match the required hole depth and hammer size. The DrillAir range allows users to choose the right compressor for their core business with the added flexibility of being able to adapt to changes in well depth and hammer size for custom applications.
All large DrillAir compressors (V900, XATS 1200 and XAVS 1000) incorporate Atlas Copco’s Pressure Adjusted through Cognitive Electronics (PACE) and DrillAirXpert technologies. The PACE technology is a software package that allows the end-user to tap into the electric engine to control pressure and flow, enabling multiple pressure and flow settings which helps operators match air flow and pressure according to specific application needs. The advantage of having multiple pressures out of a single machine, is that it eliminates the need for multiple machines.
The DrillAirXpert 2.0 is designed to allow operators to run the DrillAir at various flow and pressure settings with up to 30% improved drilling speeds. The performance management system includes software (Dynamic Flow Boost, Dynamic Control and XPR) as well as hardware (Xc4003 controller, electronically controlled inlet valve and a variable minimum pressure valve). The Dynamic Flow Boost is said to provide up to 4 m3/min additional flow when flushing and during drill stem refill and is capable of achieving 10% more flow at lower working pressure for larger diameter drilling. Key benefits include quicker flushing, faster stem refill and a shorter time to complete drilling, providing customers and end-users enhanced control on site and boosting productivity. Atlas Copco says that its Extended Pressure Range extends the working pressure range while setting it as low as 15 bar.
Stanford points out that the combination of DrillAirXpert technology with the Atlas Copco screw element and the Cummins Stage III engine, provides high efficiency for a wide range of pressure and flow settings. The FuelXpert system ensures efficiency at partial load with an additional fuel filter for better engine protection.
A 500-hour service interval helps to ensure low maintenance and operational costs. The machines’ centralised drain and air filtration systems facilitate servicing, and the oil separator system also helps reduce maintenance time. A dedicated service door allows for convenient oil level observation and oil filling, while the three-layered protective coating of zincor, primer and powder helps prevent corrosion. The machines have a short 4.1 m frame, allowing for easily transportation and a small footprint.
The DrillAir range comprises the XATS 1200, XAVS 1000, V900, X1300, V1200 and Y1300 and is suited to a range of applications including geothermal drilling and construction, blast hole drilling and exploration (mining) and pipeline, well services as well as aerated drilling (oil and gas).