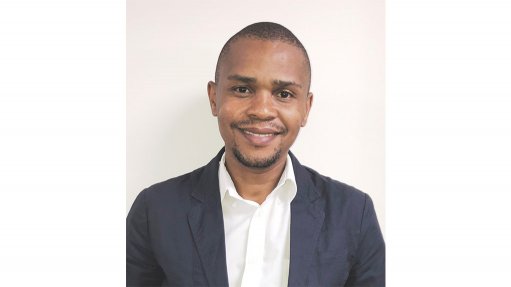
The SAGwise™ total process control solution for semi-autogenous (SAG) mills – developed by FLSmidth – promises effective SAG mill optimisation with lower energy consumption and wear part costs.
Winston Mokoena, key account manager at FLSmidth, highlights that the solution reduces critical impacts inside the mill by up to 45%. This adds life to wear liners and grinding balls, helping to prolong liner life between maintenance and giving mills more uptime.
“SAGwise can improve mill production by 6% and substantially reduce process variability,” says Mokoena. “This ensures that the mill provides a constant and optimal feed to the next stage of the process, effectively facilitating better performance of downstream operations.”
Among the challenges that mill optimisation tries to address is too little material in the mill, or too much. Too little leads to critical impacts between the grinding media and the mill liners, damaging both elements without producing value. If the mill is over-filled with mined material, on the other hand, this results in grinding inefficiencies.
The SAGwise system uses four or eight unidirectional or bidirectional audio sensors located in close proximity to the mill, which detect the analogue sounds and convert them into digital signals for analysis by a processing unit. This unit uses the sound patterns and other process variables to determine the necessary adjustment to the mill’s feed, speed and pulp density.
So direct are the improvements that can be achieved by this solution that customers can pay back their investment in less than six months, depending on the commodity value and the specific mill environment.
“The parameters that are monitored by SAGwise include the mill’s power consumption, load impacts, mill load and pulp density,” he says. “The system then responds to these parameters by controlling the mill speed, the feed rate and the water to achieve the ‘sweet spot’ where the mill runs at optimum efficiency.”