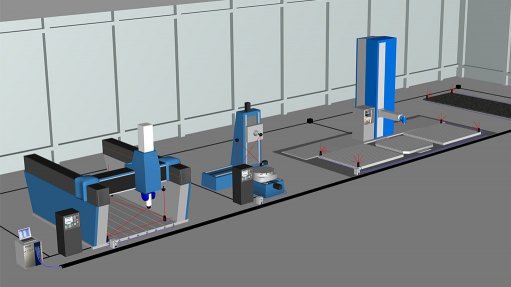
Self-correcting machine tools that not only manufacture parts, but also check the parts’ dimensions – with the Absolute Multiline Technology, the vision of a self-controlled production becomes reality. A demo of this smart technology for creating metrological networks will be given at the Control show in Stuttgart/Germany.
Absolute Multiline Technology is a world-wide unique measurement system for monitoring the geometric accuracy of machine tools by means of high-precision length measurements: An absolute distance interferometer measuring with sub-micrometer resolution serves as metrological centerpiece of a factory. It connects with any number of machines via fiber optic network that may comprise more than 100 measurement channels. These measurement channels, equipped with miniature optical elements, are oriented along the machines’ axes, space diagonals and face diagonals of the machine working volume.
Absolute Multiline Technology’s metrological network is ready to cover any machine location and size – it has already been set up in factories supplying multiple machine tools with up to 12 meters (≈39 ft.) in axis length. The maximum range of measurement is 40 meters (≈131 ft.), while the optical fibers may travel several kilometers. Due to the large distances possible between the robust measurement sensors and the system electronics, measurements can be conducted under extremely rough environmental conditions.
Better dimensional accuracy of both part and machine tool
With such integration into a machine tool, Absolute Multiline Technology can continuously monitor the geometry of the machine and initiate machine compensation in order to ensure the dimensional accuracy of the manufactured parts. To perform a standard-compliant machine tool check, a reflector from the tool magazine is interchanged, and a predefined program is executed at the push of a button to move the machine along the multiple measurement beams and thus identify their deviations. This test process takes approx. 20 minutes. Measurement uncertainty (95%) is specified with 0.5 µm per meter.
While conventional interferometers can only work with a continuous measuring beam, the Absolute Multiline Technology can deal with interruptions of its eye-safe infrared beam at any time without losing accuracy. The absolute distance is re-calculated in a fraction of a second. Hence, highest geometric precision is assured in the entire working volume of the machine. Thermal influences, wear, or collision-induced changes are reliably detected and compensated, if necessary. The machine’s geometric compensation is effected in a fully automatic way. Geometric compensation values of the machine are calculated by the software by comparison of the coordinates indicated by the machine and the length measured by the interferometers.
Thanks to the machine tool’s autonomous geometrical verification in the entire working volume, it may also be used as coordinate measuring machine to inspect the manufactured components. Especially for the quality assurance of large parts, this generates significant commercial benefits: A separate coordinate measurement machine and also time consuming clamping and re-clamping processes can be omitted.
Traceability
The metrological traceability of the Absolute Multiline Technology is ensured by the reference to fundamental physical constants: In every measurement, the molecular absorption spectrum of a gas cell is scanned, that stays constant over decades.
Presentation at Control show
Etalon showcases the Absolute Multiline Technology from 26–29 April 2016 at Control in Stuttgart/Germany (hall 3, booth 3215).