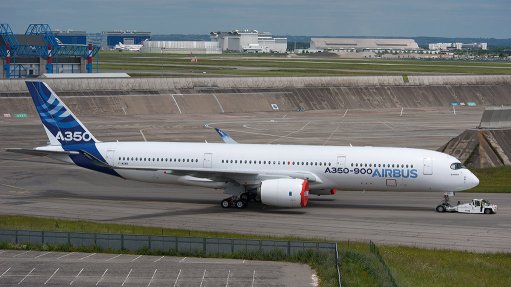
KEY COMPONENTS MADE IN SOUTH AFRICA Airbus’s latest airliner, the A350-900
Photo by: Airbus
European airliner manufacturer Airbus expects to double its current sourcing volume from South Africa by 2020. This was recently revealed in Toulose, France, by Airbus international cooperation analyst Tina Rose. Currently, Airbus sources components and parts from South Africa worth $35-million a year. Companies that are Airbus partners and suppliers are Aerosud, Cobham South Africa, Denel Aerostructures and AfricaNDT.
“Airbus has been multinational since birth,” she highlighted. “Anyone in our industry has to work globally to succeed. Ninety per cent of our Airbus business is outside Europe. We work in the medium and long term to establish business relationships that are beneficial to everyone.” Industrial partnerships with other countries bring four high-level sets of benefits: access to resources (which can be intellectual as well as material), access to markets, improved cost competitiveness and improved management of currency risks. These benefits work at all levels of Airbus’s operations and contribute to meeting all customer expectations and so achieve profitable growth.
Rose summarised the history of the current South African aerospace industry as starting in the 1960s (to digress: there were several false starts before this time, particularly in the 1930s and 1940s) with a focus on self-sufficiency. But this involved only a limited quantity of work, and so was potentially not sustainable in the long term. By the late 1990s, the industry was beginning to emerge on the international market, but remained hampered by the limited volume of work. Over these 30 years, there had been only limited South African design input. From 2001 on, the industry started to become globalised, developing links with Airbus and Boeing. With Airbus, from 2005 on, South African industry became involved in the risk-sharing design and construction of major components for the A400M airlifter programme. Today, the industry is establishing itself in technology-driven niches, which bring security.
South African manufacture of parts for Airbus aircraft started with Aerosud making flap track cans for the A320 family. Since then, the South African company has added the manufacture of detailed wing parts and avionics racks for A320s and flap track cans and carbon-fibre-reinforced plastic frame clips for A350s. Cobham makes high gain satellite antennas for most Airbus aircraft. Denel Aerostructures has designed and builds wing/fuselage fairings (WFFs), fuselage top shells and, now, vertical tail plane spars and swords for the A400M. Rose reported that the WFFs are the largest aerodynamic structures ever produced in South Africa. “It’s a complicated part,” she noted. Aerosud designed and makes many of the A400M’s internal fittings, including bulkheads and the wing tips.
The European group is also involved in research and technology (R&T) cooperation with South African institutions. In 2006, Airbus signed a memorandum of understand-ing with the Department of Science and Technology. In 2007, the European group started cooperation with the Department of Trade and Industry, the National Aerospace Centre (Airbus provides some of the funding) and South African universities. In 2009, the company signed an R&T framework agreement with the Council for Scientific and Industrial Research (CSIR).
Since 2007, the airliner company has launched a number of R&T projects with the CSIR. These cover natural fibres develop- ment, fuel slosh modelling, titanium cooper-ation and, since last year, additive layer manufacturing (this last project particularly involves the National Laser centre and Aerosud). The development of titanium additive manufacturing is a particularly important project for both sides.
This year saw the start of a new project involving Airbus, South African Airways, the Civil Aviation Authority and the Air Traffic Navigation Service. This covers the development of a new air traffic navigation and management procedure to avoid congestion in high density airspace, providing better, continuous approaches to airports (instead of stacking aircraft). In turn, this will save fuel, cut costs and reduce emissions.
“Cooperation brings added value to the country,” affirmed Rose. “We are confident about continuing our work with our partner-ships in South Africa.” • Keith Campbell visited Airbus head office in Toulouse as a guest of the company.