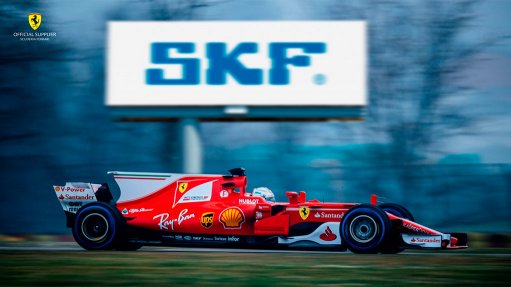
In Formula 1, weight, friction and unexpected failures are enemies of high performance, and every detail matters. With a long history of providing superior solutions to aid superior performance, SKF’s work in the sector continues to be highly specialised.
The foundations of Formula 1 can be traced back to 1946, when it was defined to be the premier single seater racing category in worldwide motorsport. SKF has been a leading supplier of bearings for Formula 1 vehicles since the early days of its inception. Indeed, the company prides itself on not only its durable solutions but also its enduring relations in the sector – its technical partnership with Scuderia Ferrari stretches back to 1947, for example.
With dedicated application engineers supporting most of the major teams, SKF products are used throughout the car. It provides ball, roller and plain bearings for wheel hubs, gearbox, clutch, engine, turbo, MGU and suspension components, as well as specialised support equipment, like high-speed condition monitoring systems to track component performance.
“The products we provide for Formula 1 teams are all 100 per cent customised for the individual application,” explains Andrea Rifici, SKF application engineer for Scuderia Ferrari “This is an industry where the leading players are looking for solutions that go to the absolute limits of what is possible.”
Compared with the vast majority of the company’s products, which are designed with maximum life in mind, Rifici notes that its Formula 1 customers have very different priorities. “Reliability is vital in these applications, but it is a ‘limited’ reliability: coatings and materials might need to perform properly for just five races, for example.”
A Formula 1 bearing may have a relatively short life, but it is a demanding one. They must be designed to withstand extreme loads, speeds and operating temperatures, while keeping their size and weight to an absolute minimum. That calls for exotic materials.
“We use very hard powder metals for gearbox and wheel bearings, high nitrogen steels, including our proprietary Nitromax alloy, and M50 (an extremely hard and heat resistant tool steel) for turbos,” says Jeroen Wensing the company’s Innovation Manager for Racing.
“In most cases, bearing rollers are ceramic, in order to reduce friction and save power. Cages may be made from PEEK (a high performance polymer), titanium or steel. Plain bearings for suspensions and similar applications are made in steel, titanium or even aluminium, with special liners in PTFE and ceramic coatings on the ball.”
Base materials are treated with high tech coatings to further improve their performance. The company uses manganese phosphate, diamond-like-carbon (DLC), and ceramic coatings on different bearing components. Seals and plain bearing liners are treated with special low friction coatings to help squeeze every last drop of efficiency from the car.
Even the most advanced materials in the world are no use if they can’t be supplied to meet the frenetic pace of Formula 1 technical development, so SKF has also developed special product development and production processes to support the sport.
“The speed of development is enormous compared to mainstream industry and several product updates are required over one season to improve the performance of the cars,” says Wensing. “This requires a lot of flexibility for everyone involved from product development to the factories.” Application engineers like Rifici typically have weekly meetings with the customers, and provide 24/7 support to the Formula 1 teams throughout the year.
As regulatory changes continue to push teams to improve both the reliability and efficiency of their cars, and with competitive pressures as relentless as ever, SKF’s engineers can be assured of new challenges in the seasons to come.