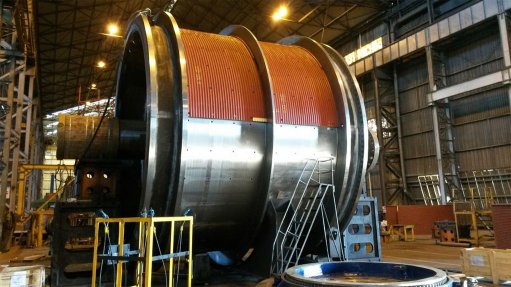
Vereeniging-based specialist manufacturer DCD Heavy Engineering – part of the DCD Group’s mining and energy cluster – is nearing completion on a two-year project to produce winder drums for a copper mine in Zambia.
The contract was for two double-drum winders for hoisting rock and two single-drum winders for hoisting personnel; the order also included related components such as clutches, bearings and brake stands and assembly.
“These are substantial items of safety-critical equipment that need to perform optimally for a life of at least 25 to 30 years with no room for error,” said Jaco Muller, project manager at DCD Heavy Engineering. “The project required not just our high levels of engineering expertise and state-of-the-art facilities, but also needed to conform to various international safety and quality standards; so leading consultancy Hatch Africa was engaged to ensure strict adherence to these quality requirements.”
The completed man-winder is 6,4 m in diameter and 204 tons when assembled, and can transport 141 people at a time to a depth of 1,9 km below surface in just over two minutes.
The rock winder – measuring 7,2 m in diameter and weighing 175 tons when assembled – collects rock from a depth of up to 2 km; each load weighs up to 27,5 tons and can be delivered in less than two minutes. The winder makes a complete revolution almost every second, and on average will deliver more than 550 tons of rock in an hour.
“Most of the steel for the manufacturing process was sourced from China, as South Africa’s local mills were not able meet the specific requirements,” said Muller. “Some 1,700 tons went into the project, made up of 125 plates ranging from 60 mm to 215 mm thick; the largest plate was 170 mm thick and weighed 30 tons, measuring 9 m by 2,5 m.”
Equipped with the largest Hauesler roll plate bending machine in Africa, DCD Heavy Engineering was able to roll the 170 mm thick plate into an almost 180 degree cylinder through a hot rolling process.
“The manufacturing aspects of the project took 18 months, with a total of about 60,000 hours being invested,” he said. “Quality was paramount, and machining tolerances were a very fine 0,1 mm on fit-up.”
The DCD Group is also active in rail, defence and marine segments, offering comprehensive and integrated heavy engineering solutions with its superior engineering expertise, world-class facilities and innovative design capability.