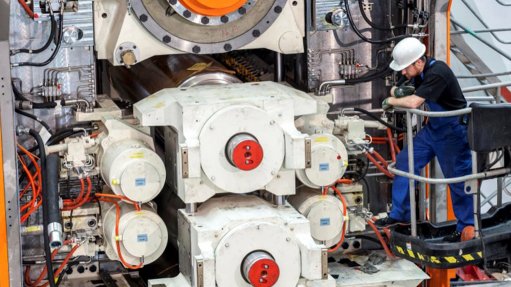
ArcelorMittal Bremen will upgrade its hot strip mill with the aid of SMS group
ArcelorMittal Bremen, Germany, has contracted SMS group www.sms-group.com to modernize its hot strip mill with the objective of improving hot strip tolerances. The upgrade will comprise the installation of a CVC®plus work roll shifting system with integrated bending mechanism and of new drive spindles in the first three mill stands of the finishing line, plus the installation of a new PCFC® (Profile, Contour and Flatness Control).
The modernization will provide ArcelorMittal Bremen with a powerful actuator to influence strip profile and strip flatness. The facility in Bremen is the third hot strip mill of the ArcelorMittal group to be equipped with the CVC®plus system (Continuously Variable Crown) by SMS group within a short period.
Axial shifting of the work rolls, that come with the special CVC®plus crown, combined with roll bending system and the technological process model PCFC® permit the roll gap to be perfectly adjusted to changing process
conditions and hence to produce strips with close geometrical tolerances. The drive spindles to be supplied to ArcelorMittal Bremen will be SIEFLEX® HT gear-type self-aligning spindles (High Torque) developed by SMS group.
SMS group is a group of companies internationally active in plant construction and mechanical engineering for the steel and nonferrous metals industry. It has some 13,500 employees who generate worldwide sales of more than EUR 3 billion.
The sole owner of the holding company SMS GmbH is the Familie Weiss Foundation. Finishing stands F1 to F3 will be modernized in two steps during the regular annual maintenance downtimes in October 2018 and October
2019. The PCFC® will be integrated before the second downtime already and run in parallel to the existing control system. Thanks to this so-called shadow mode, it will be possible to check all functions, interaction with the automation environment as well as model adjustment prior to commissioning, and finally to ensure the smooth
start of production.