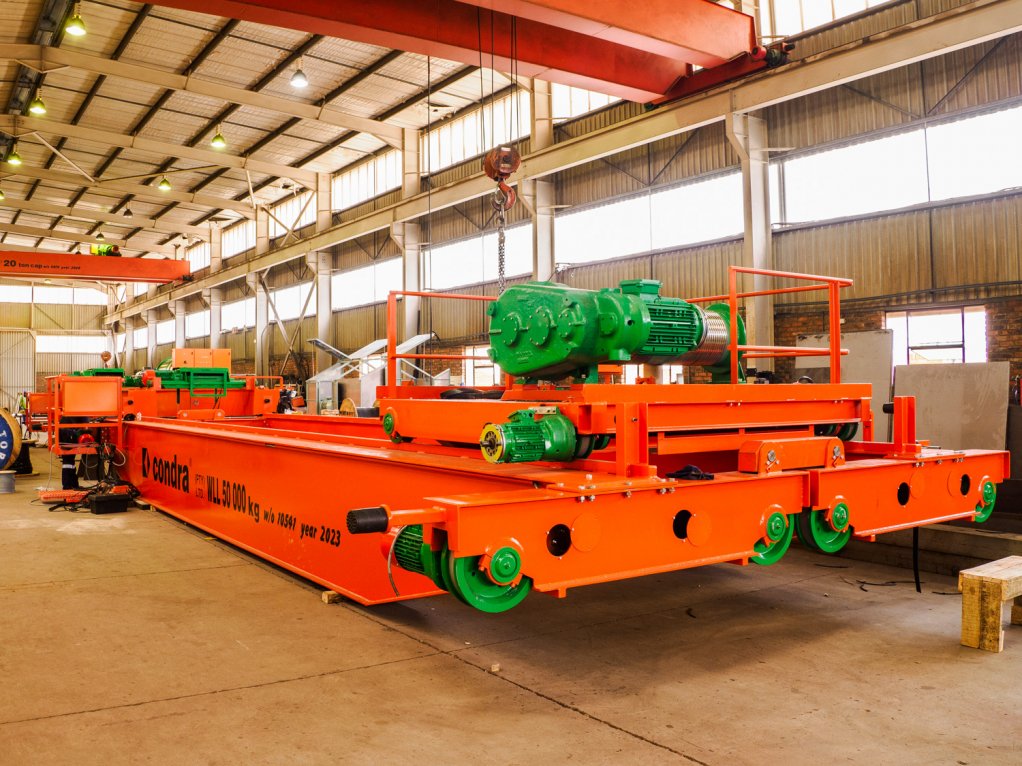
DOUBLE CHALLENGE Double bogeys fitted to the end-carriages of this overhead crane represent the key to a puzzle recently solved by Condra
Crane manufacturer Condra Cranes is preparing to embark on a crane installation to customer specifications in a factory that has no roof access and limited headroom.
The team of Condra specialists, set to undertake the installation at the customer’s Johannesburg factory this month, will leverage double bogeys fitted to the end-carriages of the overhead crane.
According to a Condra spokesperson, the installation of a crane of this type usually involves lifting the disconnected end- carriages on to the gantry first, before attaching the girders to form the frame of the crane and then lowering the crab and hoist into position from above.
“The problem in this case is there is not enough factory headroom to do that, even though Condra has designed the crane with a lowered profile to achieve maximum lifting height.”
Condra’s solution was to fit both 12-m-span steel girders with bogeys at each end – four bogeys in total – which frees up an additional 20 mm of headroom through reduced wheel loading and smaller-diameter wheels on the end-carriages, and develop a different installation sequence.
“Integral bogeys also allow placement of the girders on the factory gantry as the first step. Moving the girders apart then delivers space to allow lifting of the hoist into position between them, instead of lowering it into position from above. Closing up the girders, then linking and fixing the bogeys, result in a completed crane with two double-bogey end-carriages,” the spokesperson explains.
Meanwhile, Condra also designed an “unusually large rope drum” on a hoist to hold and manage nearly 700 m of rope, winding and unwinding it at high speed during very high lifts of 150 m within a narrower-than-normal mineshaft.
The focus of the drum’s design was a careful calculation of rope drum dimensions and winding sequence.
“Drum pitch-circle-diameter (PCD) is 1 600 mm. A 4:2 centre-lift reeving arrangement will avoid snagging the mineshaft sides,” the Condra spokesperson said in a statement to Engineering News & Mining Weekly.
The drum, which is nearing completion at Condra’s Germiston factory, will carry 676 m of 18 mm rope, lifting and lowering loads at 30 m a minute, which is nearly ten times faster than lifts in standard overhead crane workshop applications.
“Condra’s design team had to coordinate the drum width with a PCD and reeving arrangement that will precisely control and restrict lateral movement of the four ropes moving vertically as they lift or lower the load.”
The rope will wind on to or unwind from the drum in opposite directions as the drum rotates.
The hoist features improved drives, gearboxes and safety devices and enhanced operation by remote control, while the motor design is such that the load placed on the electric motor will remain manageable despite the nonstop nature of the work at the mineshaft.
Crab span is 6 972 mm with a wheelbase of 3 400 mm.
The crab and hoist disassemble to fit into a standard 12 m shipping container.