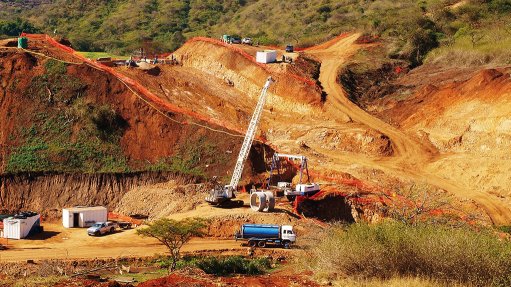
MAKING PROGRESS The crane and gantry are in position for the pipe-jacking operation
Work is well under way on the R212-million Imvutshane dam, 30 km north-west of Stanger, in KwaZulu-Natal, which is a key link in supplying people in rural Maphumulo with a reliable source of safe drinking water.
Currently, more than 50% of the Maphumulo population are without any formal water supply and the remainder depends on unreli- able small water schemes. Further, during winter and droughts, water is scarce through-out the region.
According to agriculture engineering con-sultancy MBB Consulting Engineers, which was appointed by State-owned water utility Umgeni Water to design and supervise the construction of the 3.1-million cubic metre dam, completion is scheduled for February 2015.
“Excavation on the spillway has been com- pleted and, to increase its depth by an addi-tional 8 m, two small blasts have been successfully carried out. The outlet pipe has been jacked through a rocky hillside and 50% of its 106 m journey has been completed,” says MBB project engineer Tyler Bain.
Umgeni Water, the bulk water supplier to the Ilembe district municipality, in Stanger, is implementing the extensive R402-million Maphumulo Bulk Water Supply Scheme. This includes the construction of the Maphumulo Water Treatment Plant, an extensive network of pumpstations, bulk water-supply pipelines, reservoirs for treated water and the construc-tion of the Imvutshane dam.
The design of the dam offered some interest-ing challenges. Geological studies showed that the rock was badly weathered in the area designated for the spillway. MBB designed a concrete-lined spillway that will be anchored into the ground; this is a safety measure to ensure the dam can withstand extreme floods.
“The 28-m-high, 305-m-long embankment will be built using different construction methods. A section will be clay core and the remainder will be built of compacted earth, with a rock shell. Sufficient clay and rock have been sourced on site, so the amount of materials which have to be transported is minimal,” added Bain.
Another challenge was a pothole, situated where the dam crosses the river, which was unsuitable as a foundation. Mitigation jet grouting will be used to create a strong, water-tight foundation for the dam’s embankment.
This entails drilling into the ground and creating columns of soil and cement by intro-ducing cement grout at high pressure. A series of underground, overlapping columns will be constructed to form an impervious wall of up to 16 m in height.
“The pothole also caused foundation chal-lenges for the outlet pipes. MBB solved the problem in a fairly cost-effective way by jacking the pipes through the adjacent hill. A powerful hydraulic jack is being used to push a concrete pipe 106 m through the rocky prominence. While the pipe is being driven through the ground, behind a shield, excavation takes place,” says Bain.
To ensure the concrete sleeve is watertight, the gap between the pipe and the rock will be sealed with cement grout and the rock will be grouted at specific places. The outlet pipes will be fitted inside the concrete sleeve and will divert water away from the site during construction, while continuing to supply water to the treatment plant.