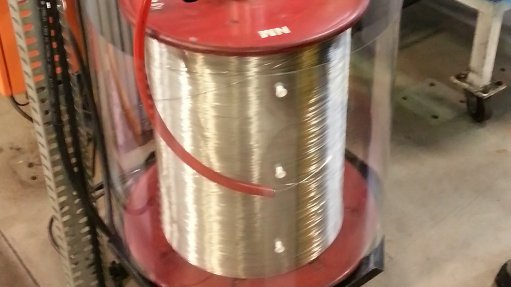
STAINLESS STEEL WIRE Wire Products Stainless Steel has been manufacturing stainless steel MIG wire locally since late 2010
Stainless steel bar and wire producer Wire Products Stainless Steel (WPSS) can now manufacture stainless steel MIG welding wire on 15 kg wire baskets for hand-held and robotic welding systems, WPSS director Clinton Lautenberg tells Engineering News.
This has enabled the company in the past two to three years to supply materials to large international catalytic convertor manufacturers and assembly plants.
WPSS has been manufacturing stainless steel MIG wire locally since late 2010, which includes the 430LNB, 307Si, 308Lsi, 309L, 309Lsi, 310 and 316Lsi grades.
“The addition of the MIG welding wire fits seamlessly into our production capabilities and has assisted us in improving the quality standards and procedures for all our other products,” he adds.
Lautenberg says the wire was initially produced only in bulk packs using the Novametal Megareel payoff system.
“The system is designed to supply tangle-free wire to robotic welders, specifically in the automotive industry for catalytic converters.”
Lautenberg stresses that the production processes follow the same strict quality procedures as those of its holding company, Swiss-headquartered Novametal SA. All wire manufactured by WPSS conforms to American Welding Society and ASTM standards and is used by heavy and light engineering, and fabrication industries.
“WPSS has refocused its manufacturing facility in the past 18 months to perfect the core products that have been the lifeblood of the company for the past 20 years, namely 2.5-mm- to 30-mm-diameter round bar as well as general wire, welding rods and wire for specific applications,” he points out.
Facing Up to Challenges
Lautenberg says the company has been affected by the global downturn in manufacturing, as mills worldwide have large amounts of spare capacity and are aiming to secure export business to fill this capacity.
He explains that although South Africa’s market is miniscule with regard to the global consumption of stainless steel, it has, however, been a traditional target for global stainless steel mills, as the laws protecting local manufacturers in South Africa are not as strict as those in Europe or North America.
“Imports from the east, namely India and China, have put severe pressure on margins for locally produced product. While these pressures exist, we have been fortunate to receive strong financial and logistical support from our holding company Novametal SA,” he emphasises.
Lautenberg highlights that additional challenges faced by the company include the weaker rand, labour unrest and unrealistic wage demands across not only the metal industry but also the industries that use stainless steel such as the mining and automotive industries.
“To combat these challenges, WPSS streamlined all its procurement, manufacturing and distribution processes to compete with cheap imports. We have to improve efficiencies and decrease costs,” he stresses.
Moreover, Lautenberg says that buying higher-quality raw materials at a lower price from reliable raw material suppliers has enabled WPSS to hold less stock and produce high-quality finished product with higher yields.
“The stainless steel industry is definitely under pressure and volumes have decreased significantly in the past two to three years,” he laments.
“However, despite these challenges, WPSS is determined to retain its status as a world-class manufacturer and distributor of stainless steel wire and round bar, not only for the South African market but also for the export markets,” concludes Lautenberg.