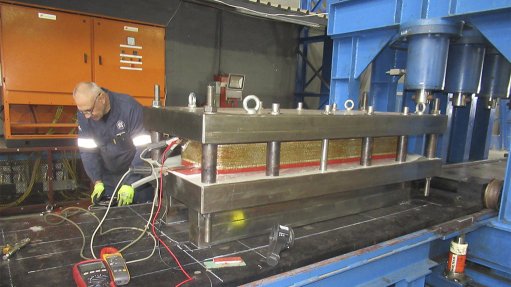
POLE POSITION Marthinusen & Coutts was tasked with the challenge of reverse engineering the poles and coils for a hydroelectric power station in Cameroon
Electric motor repair service provider Marthinusen & Coutts finalised the manufacture and delivery of four new replacement field coils and poles for a 25 MVA 36-pole generator at a hydroelectric power station in Cameroon.
Finalised in September, the order, booked in June, for hydropower project manager Voith Hydro in Africa, entailed the full development of tooling and jigs specially designed to suit the manufacturing needs for the coils and poles.
“We are often called upon to manufacture items by applying reverse engineering procedures when the original-equipment manufacturers design drawings for the equipment are unavailable,” says Marthinusen & Coutts works executive Craig Smorenburg.
However, the greatest challenge on this project was the fact that the original coils and poles had been stolen from the site and could not be used as templates for the reverse engineering.
He explains that Marthinusen & Coutts were provided with rough dimensions, which were sufficient for the quotation process, but not accurate enough to successfully design and manufacture the parts.
Additionally, the field coils were of a complex design that consisted of a double- bank series coil with a unique method of connection between the north and south poles.
“Another unusual feature was that the copper dimensions required on-edge bending to wind a continuous coil,” Smorenburg stresses.
Consequently, the decision was made by Marthinusen & Coutts to send two senior technical staff members to the 264 MW Edéa power station on the Sanaga river near the town of Edéa, in Cameroon to try and obtain more accurate dimensions and any other information that could be gathered.
“The staff members managed to attain useful photographic evidence, along with the more reliable dimensions,” he adds.
The design of the tools and jigs was then taken on over a 25-day period, before the manufacture of the coils and poles started.
The manufacturing process was undertaken at Marthinusen & Coutts power generation and large motor facility in Benoni, which had been tentatively prepared for the manufacture while accurate dimension and drawings were acquired.
All parts were then shipped by air to Douala Airport, before being transported by road to the site in Edéa 63 km away.
Smorenburg concludes that Marthinusen & Coutts prides itself on the fact that all the manufacture was assumed, and all materials were sourced locally.