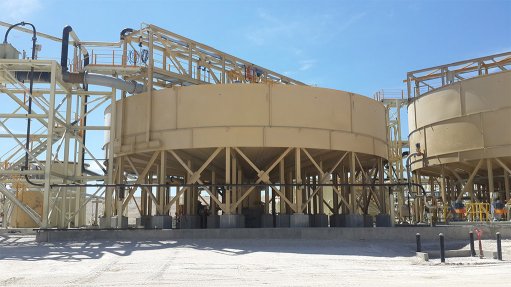
The concept of bolted thickeners is growing in popularity. According to FLSmidth senior account manager Ricus van Reenen, this is a fit-for-purpose, high quality dewatering solution with reduced project construction risk and duration.
These benefits resulted in FLSmidth securing an order in July 2017 for a 24 metre diameter high-rate thickener from a South African iron ore mining company.
“Although this concept has been around for at least a decade, it is becoming more commonly used,” says van Reenen. “With a bolted tank, the whole thickener is constructed inside a purpose-designed fabrication facility with all welding, sandblasting and painting taking place under controlled conditions. This guarantees that everything fits as it should so there are no unexpected delays on site.”
Thickeners have traditionally been constructed on site; all rolled and bent plates are transported to the required location where they are welded onto the prefabricated support structure and radial beams.
“This process can take weeks to complete, as there are kilometres of welding runs required,” he says. “Moreover, the considerable weight of the material in the finished tank – several thousand tonnes – means that the weld quality needs to be high and coded welders must conduct the work.”
These welders often have to be accommodated on site for extended periods of time, which adds to the cost; cross-border work often involves the added burden of obtaining work permits and special visas for these workers.
Sandblasting of the welding runs is then necessary, as well as a final coat of paint. In addition to the extra costs, the work is highly weather dependent and delays can be caused by rain or excessive dust.
“Weather related delays can cause time over-runs for the contractor, which can then lead to penalty costs,” he says. “This sort of project risk is one of the main reasons why contractors are choosing bolted thickeners. As a contractor, your time on site is where your most significant risk will lie.”
After the construction of a bolted thickener in a workshop, the whole tank can be transported to site where the bulk of the on-site work can be undertaken by a mechanical supervisor, who oversees the lifting and placement with the support of a rigger and a crane driver. Local labour can be used to fit the necessary bolts into the structure, and a technical specialist can come in to torque the bolts.
“Once in place, only touch-up painting is required, so poor weather won’t be a serious risk factor,” says van Reenen. “Ensuring that deadlines are met means on-time commissioning, which aligns well with FLSmidth’s role as productivity partner to mining projects.”
He notes that FLSmidth has supplied at least 20 projects globally with bolted thickener tanks, putting close to 40 of these units into the market in recent years. The largest unit was a 45 metre diameter high-rate thickener, while the more specialised deep cone thickeners have also been built in this way up to a size of 35 metres in diameter.