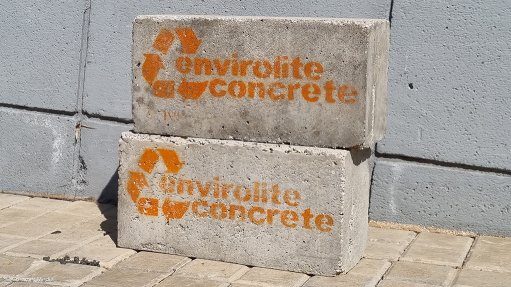
Envirolite polystyrene-derived construction block
Photo by: Creamer Media's Marleny Arnoldi
Automotive manufacturer BMW South Africa has expanded its BMW Information Technology Hub (IT Hub) services to include digital twinning for all newly produced plug-in hybrid and fully electric vehicles across the group.
The exercise adds to BMW’s ambition to be the most sustainable car company in the world.
The IT Hub, based in Pretoria, provides digital communication and technology services used internally by employees and plants of the global BMW group.
The hub, through its 2 300 employees or “hubsters”, exports knowledge to more than 70 countries where BMW has operations. The hub has employed an average 400 new people every year since 2019.
The Digital Vehicle File, or digital twin, offering serves as a foundation for documenting changes to the vehicle over its lifecycle and includes information on each and every component within the vehicle – including the amount of metals contained in the battery, for example.
The digital twin has information on materials, parts, serial numbers, battery production, vehicle data, after-sales data, software data, car configuration and supplier data.
BMW South Africa IT Hub digital director Thorsten Achenbach explains the rationale for the digital twinning of vehicles as being the ever-increasing stringent markets of China and Europe to track, trace and quantify materials contained in electric vehicles.
The Digital Vehicle File also enables more efficient recycling when a vehicle reaches the end of its lifecycle, thereby enhancing BMW’s circular economy.
More than five-million vehicles have been logged using the Digital Vehicle File system.
As demand for battery materials is poised to reach $4-trillion in value up to 2050, Achenbach deems it crucial to keep track of and reuse these materials, particularly as less than 9% of these resources are currently recycled or reused.
“The BMW Digital Vehicle File serves as a single point of truth for vehicle data including sustainability data, in close collaboration with industry platform Cantena-X, with hardware, software and feature data being compiled over the entire product life. This enables innovative mobility concepts and cost savings, while meeting regulatory requirements globally,” Achenbach adds.
ZERO WASTE
BMW South Africa, meanwhile, achieved zero waste to landfill in May 2021, compared with having disposed about 915 700 kg of waste to landfill in 2018.
In particular, BMW South Africa has avoided wasting 244 t of polystyrene since May 2021, by collaborating with Envirolite to manufacture lightweight concrete-like construction blocks used to build low-cost housing and other structures.
Another example is BMW South Africa’s organic waste going to local worm farms as feedstock.
The company has, since 2015, sourced electricity from a biogas plant through an agreement with energy company Bio2Watt. This has helped the Rosslyn plant to reduce carbon dioxide emissions by more than 2 036 t between 2018 and 2022.
Additionally, BMW South Africa managed to reduce its energy consumption by 17 603 MWh from 2018 to 2022, as well as its water use by 126 095 m3 over the same period.