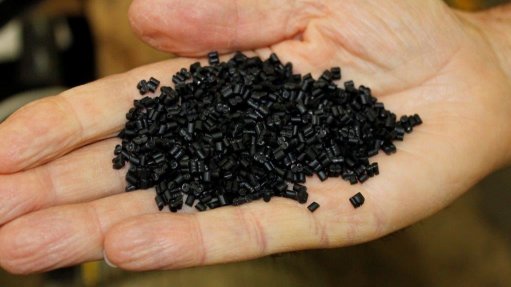
PELLETISEDPolypropylene is pelletised and shipped to the plastics factory for further production for which it will be used in new batteries
South African manufacturer and distributor of lead acid batteries First National Battery, a subsidiary of JSE-listed Metair Investments, has committed to environmental sustainability and has consolidated its operations by commissioning a polypropylene recycling plant at its Benoni factory, in Gauteng.
Construction of the recycling plant started in March and was on line by the end of April.
The company’s lead smelter has been producing high-quality alloys for more than 14 years and the establishment of the polypropylene component of the recycling plant completes the vertical integration of its battery production processes, says First National Battery MD Dr Louis Denner.
Polypropylene is used to manufacture battery cases, lids and other components of various batteries. Automotive battery components include lead, plastic and acid, which are harmful to the environment if they are not properly treated.
Most of the harmful components are recyclable, which has become an important consideration for First National Battery, not only to recover valuable materials but also to protect the environment, says Denner.
He adds that the manufacturing of lead acid batteries in South Africa depends on the recycling of lead and polypropylene. The whole battery is recycled and the process begins with breaking down the old battery and recovering the lead and polypropylene. The lead is smelted while the polypropylene is converted into granules, which are then washed, dried and pelletised. The polypropylene pellets are bulk-shipped to First National Battery’s plastics factory in Fort Jackson, near East London, where they are combined with a specific ratio of virgin material to ensure sufficient tensile strength.
Complete vertical integration enables First National Battery to oversee the entire process – from the recycling of old batteries to the recovery of materials and from the production of new plastic components and high-quality lead alloys to the assembly and distribution of new lead acid batteries. “This ensures that tight controls are consistently implemented to guarantee that the highest-quality products are manufactured using the best raw materials available,” concludes Denner.