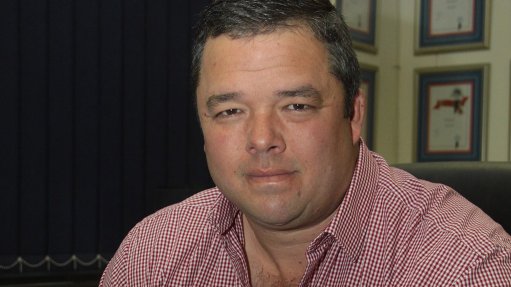
The tough construction and proven operating principle of AWS, AWD & AWL liquid ring vacuum pumps from Atlas Copco make them suitable for use in the most demanding of environments across all sectors, from food processing and petrochemical to construction.
Pre-engineered and fully assembled plug-and-play solutions, with one or two stages, in three different standard configurations, these pumps deliver resource-conserving plug-and-play solutions that save costs and improve productivity for end-users.
Liquid ring vacuum pumps combine a sturdy, reliable and low-maintenance design with highly efficient performance and silent running. These pumps are also extremely well suited for humid, wet or corrosive process flows and even tolerate particles with ease. Users benefit from short lead times, minimum life cycle costs and high reliability.
Liquid ring pumps are equipped with a fixed blade impeller located eccentrically within a cylindrical casing. As the impeller rotates, liquid (usually water) is thrown out by centrifugal force to form a liquid ring around the circumference of the casing, sealing the tips of the impeller and creating separate enclosed gas chambers between each blade. As a result of the eccentric position of the impeller, these chambers vary in volume as the shaft rotates, having the effect of drawing in and compressing process gas.
The AWS and AWD vacuum pump series are offered in three pre-engineered modular configurations designed for once-through, partial recirculation or total recovery of the service water. Striving to make the customer’s life easy Atlas Copco offers all three configurations as pre-fabricated plug-and-play modules, including pump, motor and water recirculation system mounted on a compact skid.
Customers receive a complete solution which can be easily installed and commissioned with the minimum amount of work. In most cases all wetted system components are manufactured from stainless steel.
The module with the simplest design is the once-through pump which consists of a pump with electric motor, drive system and skid. It is ideal for installations with an adequate supply of site water available which can then be continuously drained from the pump for re-use. The pumping system adds no contaminates to the service water other than those coming from the process.
In the case of partial recovery, the discharge liquid-process gas mixture is collected in a vessel where it is mixed with fresh sealing liquid to ensure a constant temperature in the pump. Excess liquid is released from the system via an overflow. Compared with once-through operation, this mode of operation typically saves 50% of the fresh water required.
With total recovery, liquid savings of up to 95% are possible. The recovered liquid is cooled via a high efficiency heat exchanger before being returned to the pump chamber. This configuration works with a closed liquid cycle and is recommended because it physically separates the cooling water circuit from possible process contaminates.
Capacities range from 170 to 37,500 m³/h. Lower capacity (below 5500m3/h) units are available as single-stage AWS models or two-stage AWD models preconfigured with direct-drive options in 50 and 60Hz speeds. Single stage AWS pumps have outstanding efficiency above 200mbara, making them ideal for general process applications such as filtration and dewatering, and pump down or evacuation duties.
The two-stage AWD pumps provide constantly high performance at operating pressures below 200 mbar (absolute). Two synchronized pump chambers work in series to achieve high performance and improved efficiency on continuous process duties such as drying, degassing exhausting and solvent recovery.
For larger installations, belt or gearbox transmission high capacity AWL pumps can often be the most appropriate selection.
All AWS and AWD pumps achieve class leading ultimate pressure levels as low as 30 mbar (absolute).
Pre-engineered standard configurations allow for fast response to customers with proven technology solutions based on years of experience and best practice design. For more complex projects, Atlas Copco’s applications teams develop systems tailored to meet customers’ unique requirements. Atlas Copco experts can offer liquid ring packages adapted to most process conditions, including special materials and design of multi-stage systems.
In addition, Atlas Copco can develop and design systems suitable for operation in potentially explosive atmospheres in accordance with ATEX.
Testing to Pneurop and HEI standards along with material certifications, project support and approved quality plans are also offered by Atlas Copco. Furthermore, the company’s electrical engineers have experience with the design and installation of control systems for intelligent pump management.
The simple and sturdy design of these pumps make them ideal for the reliable delivery of vacuum in humid, dusty and dirty environments typically found in industrial processes across a wide spectrum of industries including food & beverage, dairy, mineral processing and mining, chemicals and petrochemicals, pharmaceuticals, oil, steel, cement, plastics, paper & pulp and textiles.
Atlas Copco introduced its new AWS and AWD series standard liquid ring vacuum packages at ComVac, held in Hanover at the end of April 2017.