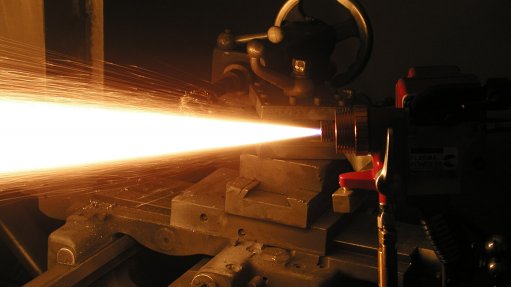
IMPLEMENTATION IMPERATIVE Implementing industry standards will enable end-users to insist that companies show that their thermal spray operators are certified
The Thermal Spray Association of Southern Africa (TSASA), a subcommittee of nonprofit technical organisation the Southern African Institute of Welding (SAIW), aims to increase thermal spray use while improving standards in local industrial sectors.
TSASA chairperson Adam Wintle tells Engineering News that the association met with provider of standards, management systems, business improvement and regulatory approval information the South African Bureau of Standards (SABS) last month about locally implementing and enforcing certain internationally recognised thermal spray standards.
These standards include ISO 14923:2003 – which specifies an overview of the characteristics of coatings produced by thermal spraying – and ISO 9001:2008 for a quality management system. Wintle highlights the importance of the latter, as companies need to demonstrate the ability to consistently provide products that meet customer and applicable statutory and regulatory requirements.
He explains that the implementation and enforcement of standards in the thermal spray industry is “critically important”, as the production and use of substandard thermal spray products has, in the past 10 to 20 years, created a negative perception regarding the use of thermal spray products in Southern Africa.
“Implementing industry standards will [entitle] end- users to insist that companies show that their thermal spray operators are certified and, therefore, competent to apply thermal spray coatings,” he states.
Moreover, Wintle notes that he met with the German Association of Thermal Sprayers (GTS) at the 2014 International Thermal Spray Conference and Exposition, which took place in Barcelona, Spain, in May. It was agreed that the GTS would support the TSASA by providing input and guidance on ways to strengthen the thermal spray industry in Southern Africa.
The GTS will also provide training material for the TSASA once the association has established training courses locally.
“Our long-term vision is to provide training courses and certification programmes in the next five to ten years for thermal spray operators, in conjunction with the SAIW,” states Wintle.
Thermal spray coatings can be applied as wear-resistant, corrosion-protective, nonstick, dielectric, electrically conductive and thermal-barrier coatings. Further applications include hard chromium-plating replacements and coatings for food- processing equipment, medical instruments, traction control, electromagnetic interference and radio-frequency interference shielding.
Wintle states that thermal spraying also plays a significant role in the international aerospace industry, as 75% of an aircraft’s engine is covered with thermal spray coatings.
He points out that an aircraft engine’s turbine blades are typically made of high-grade metal alloys and may be negatively affected by the high temperatures produced by the aircraft’s engine.
“However, the thermal coating ensures that the blades are protected from the high temperatures and will not melt as a result,” Wintle concludes.