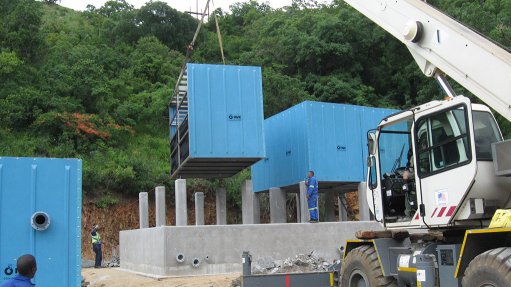
As you mine deeper, sooner or later it’s going to get hot. And so it has at Barberton, although it has taken more than a hundred years. BBE Projects have recently commissioned a refrigeration and air cooling system at Barberton Mine’s Fairview Shaft to provide much-needed cooling for the on-going expansion into the deepening orebody.
Barberton Gold Mine is a subsidiary of Pan African Resources Plc. It consists of three operations namely Sheba, New Consort and the Fairview Operation. Fairview is currently the deepest and will continue to go deeper and that is where the cooling was needed.
Fairview Mine’s Adit is located in a tranquil valley, halfway up a hillside, just outside the town of Barberton in scenic Mpumalanga.
The refrigeration plant, comprising two York R134a refrigeration machines, condenser cooling towers, pumps and electrics sits on a rehabilitated corner of the main terrace, tucked up against the hillside. The bulk air cooler (BAC) is an underground horizontal spray chamber located in an intake airway more than a kilometre into the mountain. Although on the same level as the surface refrigeration plant, the bulk air cooler is some 250 m below the surrounding hillside.
Access to the terrace is by a tortuous road with a novel α-shaped hairpin corner that challenged the tactics of the transport company for the long heat exchanger shells of the refrigeration machines and the large cooling tower components. All part of the challenge and the planning of the project. Ideally, it is preferable to maximise the fabrication and assembly work performed in the factory so as to minimise site work. For example, the refrigeration machines, from the USA, were shipped fully assembled, complete with compressors and electric motors.
Similarly, the entire electrical equipment comprising motor control centre and PLC panel could be packaged into a single container which was able to negotiate the route. However, the two condenser cooling tower cells had to be supplied in four halves to keep the module sizes manageable for transport.
The duties of the refrigeration machines were chosen to get the best balance between economy of scale, and modularity for load matching and operational redundancy.
Warm water from the bulk air cooler is pumped from the BAC, to the refrigeration machines and back, through a 3 200 m pipeline. Being a low pressure application, and predominantly in quiet intake airways, it was possible to make use of HDPE piping which has the added benefit of providing sufficient insulation properties for this particular situation. The returning cold water is pumped through two stages of sprays to maximise the efficiency of the BAC.
BBE Projects were given access to site in November 2016 and the plant was operational in July. As part of their complete turnkey project, BBE went to great lengths to maximise the use of local contractors for all civil construction and mechanical and electrical installation works.
Since the commissioning of the fridge plant the environmental conditions in the mine have improved drastically.
Management at the mine commended BBE Projects on the excellent manner in which the project was completed and the great co-operation between the contractor and the mine staff to ensure that the project was completed safely and timeously.