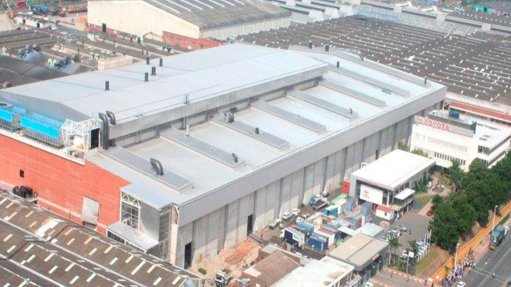
AECOM was responsible for the engineering services for a recent expansion project undertaken by Toyota South Africa Motors at its manufacturing facility near Durban. This included a new press line with the largest press in the Southern Hemisphere.
Toyota South Africa Motors recently increased the capacity of its existing press shop at its Prospecton plant, south of Durban, driven by Toyota’s new Hilux and Fortuner models. “AECOM provided all engineering services, as well as project cost control and project management, with our fully integrated team,” Stuart Manzie, Associate, Building & Engineering, AECOM, explains.
The press shop is the sheet metal shaping section of an automotive plant, which receives the sheet metal in coils. It is cut into plates of various sizes on the cutting line. These are given their final shape on presses by using different dies for each type of component, and also by means of different operations such as pulling, trimming and piercing.
The new line of presses will produce the external parts of the car body (body sides, bonnet, doors, etc.), as well as the chassis rails. The new press line consists of three new presses incorporated into an existing logistics bay. The largest of the three presses has a pressing capacity of 2 300 t, which makes it the largest press in the Southern Hemisphere.
The incorporation of the presses required the construction of new press pits for the presses, and a new scrap tunnel to house new scrap conveyors. The press shop’s die storage area was also increased to accommodate the new dies. The new die storage area has a load capacity of 10 t/m², incorporating a 500-mm-thick suspended ground floor slab supported on driven cast in-situ (DCI) piles. This also tied into four of the existing press shop bays. It included an extension to the crane runways for 40 t cranes.
The construction of the press pits and scrap tunnel required a 16 m wide by 7 m deep excavation, all within the existing building. Due to poor ground conditions and high static and dynamic loading, the pits were founded on precast piles driven down to bedrock at a depth of 40 m.
Height constraints within the building led to the piles being installed from a modified Casagrande piling rig from the bottom of the excavation. The perimeter of the excavation was shored with a contiguous piled wall using Continuous Flight Auger (CFA) piles and soil nails.
A high ground-water table meant that the bottom of the excavation was about 5 m below the water table. Dewatering wells were installed and used to keep the excavation dry. High vibration during precast pile driving and soil settlement during dewatering necessitated risk assessments to mitigate associated risks to the sensitive adjacent crane supporting structures. Weekly surveys were undertaken on building columns and floor slabs to identify any settlement that may have taken place. Vibrations caused by piling were also monitored to ensure that the specified limits were adhered too.