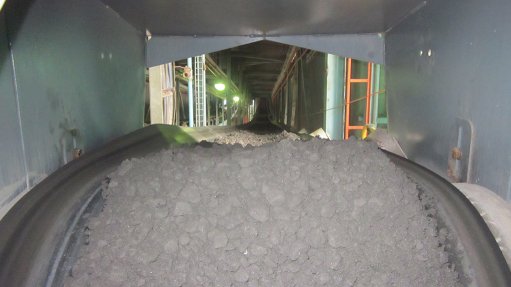
The level of performance of a mine’s transfer points contributes to some of its highest maintenance costs, but many engineers often do not consider transfer systems as critical elements of the minerals processing systems.
This is the view of Mark Baller, managing director of transfer chute experts Weba Chute Systems; he believes that transfer points should be accorded the same importance as other minerals processing machinery. In particular, the effect of the chute’s performance on the life of conveyor belts – which can account for up to 60% of the capital cost of a bulk materials handling plant – deserves attention.
“The cost of replacing a conveyor belt – not to mention the downtime associated with belt maintenance and replacement – makes it worth looking more closely at any measures that will extend the conveyor’s life,” says Baller. “Typically, conveyors – like feeders, crushers, hoppers and screens – are selected to match certain operational requirements; however, there is little emphasis on the design of the chutes transferring materials between elements.”
This is a mistake, he argues, as chutes are essential elements in a bulk solids handling plant, and are also subject to operational characteristics and physical constraints.
“Among the most common problems on transfer chutes are spillage, blockages and high levels of wear on the receiving belt due to major differences between the material velocity and the belt velocity,” he says. “There is also misalignment of the receiving conveyor belt – which is caused by uneven loading from the transfer chute.”
Key to solving these challenges is good design, he emphasises. While conventional chute design often allows the uncontrolled discharge of bulk materials, Baller considers that a holistic design is necessary – focusing not only on the entry and exit points, but also controlling the flow, volume and velocity of the material being transferred.
“Each transfer point therefore needs to be custom designed, to control the direction, flow and velocity of the material,” he says. “Weba Chute Systems bases its designs on the ‘supertube’ effect which often employs a cascade lining system – allowing 95% of material to run on other material at all times. This may also be achieved using conventional lining systems.”
He emphasises that one of the designer’s aims must be to achieve controlled transfer of material onto the conveyor belt, reducing wear and tear on belts while also minimising the impact that creates dust. The results are cost saving for customers and better occupational health and safety compliance.
“The ‘super flow effect’ is designed into our products using sound engineering principles and sophisticated 3D software,” says Baller. “We also use Discrete Element Method (DEM) simulation as a verification tool.”
The company’s design philosophy has found its way into over 4,000 transfer chute installations in mines around Africa and abroad.