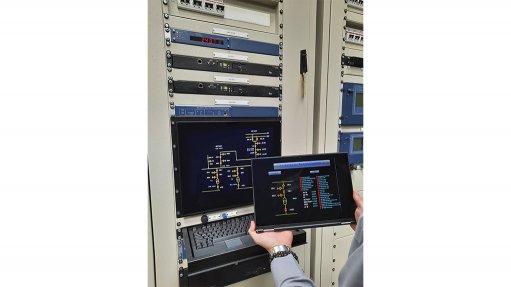
A vast array of site and engineering challenges can be resolved using advanced technology, such as Internet-of-Things devices, software programmes, artificial intelligence, and others, to enhance the predictability of asset performance in the field or within factories.
These technology-driven solutions are always designed to meet customer’s needs, focusing on increasing production, display visibility or monitoring assets or processes, with an emphasis on user friendly interfaces.
The “rapidly evolving environment” is growing exponentially, electro-mechanical original-equipment manufacturer Actom Smart Technologies (AST)’s senior GM Sy Gourrah, “AST is excited to be a part of the changes that new technologies bring to our world”.
AST is a new division within the Actom group that focuses on protection and control, devices and alternating current (AC) and direct current (DC) standby technology which also now includes solar. AST is also looking at providing new technological and digital solutions within Actom and for its customers.
“AST builds and develops solutions according to the requirements of the individual customers who have different requirements. These designs are completed by specialized engineers with vast experience. The projects are also executed by a competent team to ensure that the designs are adhered to,” Gourrah explains.
Regular testing of solutions is carried out to ensure that the products can survive in harsh African electrical and temperature environments that are often dusty, says Static technical manager Tony Gordon.
The division also builds and tests the solution so that it complies with the original design requirement, which Gordon, says requires constant communication with the end-user, via onsite service calls and direct communication with customers on issues.
Actom provides innovative turnkey solutions for renewables projects, and through the AST division, it is able to focus on the secondary equipment of these projects.
“In essence we would take care of the design, the supply, the factory acceptance testing, installation and site acceptance testing,” protection and control GM Herman Mare says.
The secondary equipment not only includes the protection intelligent equipment devices and substation supervisory control and data acquisition (Scada) system, it also includes the facility’s Scada system which allows customers to monitor and control the wind turbines or solar panels.
“As Smart Technologies, we are involved with various other projects involving new technologies to the advantage of the end customer. One such example is the use of drones to do inspections in power station boilers, cooling towers and storage tanks. This has a huge time saving advantage, as historically you would need to erect scaffolding to do these inspections, reducing the time from a couple of weeks to only a few days,” Mare explains.
He adds that this has an added cost saving benefit to the end customer as well.
“With the demand on our electrical assets ever increasing, it is no longer sufficient to protect the equipment with protection devices, and forward faulted conditions to a Scada system - technologies that Actom have employed for many years,” he comments.
He highlights that it “is now imperative to also monitor your equipment to predict possible failures or overloads and prevent it”.
Condition monitoring is extremely important to extend the lifetime of electrical equipment, such as transformers, for as long as possible.
Smart Technologies is involved in providing these tailor-made solutions, in line with budgets, for electrical equipment supplied in the market, Mare notes.
AST can provide the complete electrical requirements of the customer, and designs a custom-made product to meet needs. The complete process, depending on complexity and design, can be from two weeks to 20 weeks, and includes design, manufacture, testing, installation and commissioning.
AST’s product range serves the electrical switchgear, telecommunications, oil and gas, railway industry, municipalities, State-owned entities, private developers and independent power producers.