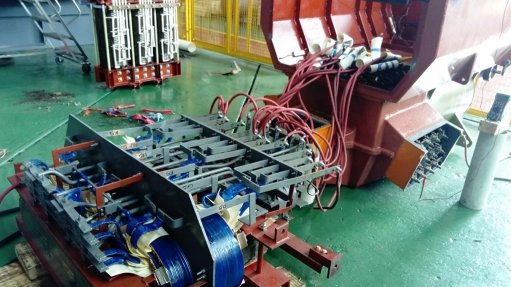
The induction regulator had failed entailing the manufacture of a new 3.3 kV 330 kVA line transformer and the rewind of both the stator and rotor windings of the induction regulator.
History of the Rotating Machine Application:
The induction regulator’s conceptual design was put forward in the 1930’s with a patent granted to Benno Schwarz in the following decade. In the days where power semiconductors were not available for AC variable speed applications, these units provided solutions where there was a requirement for high power variable speed applications. The products successfully competed with the variable speed DC generator excitation systems, in the post-war infrastructure rebuilding program. The Induction Regulator AC variable speed solution provided a reliable and efficient rotating machine operation with step-less speed variation over the desired speed range.
The reliability of operation and maintenance of the equipment has translated into their extended operation in a number of industries. The improved efficiency of the AC commutator motor combined with the induction regulator for variable speed applications is inherent in its slip energy recovery magnetics design.
The OEM of the supplied rotating equipment has long discontinued support on these products, with the result that the clients have to find alternative sources to keep their equipment operational since these tough economic times make replacements difficult.
The induction regulator that LH Marthinusen had to rebuild consisted of an energy recovery and phasing line transformer, a stator and a rotor whose angular position can be mechanically adjusted. This particular model of size 330 kVA had a 36 circuit configuration that had to be reverse engineered due to the lack of data of the aged unit.
The phasors were plotted and calculated to verify the winding phase relationships for the required manufacture of the line energy recovery transformer. Furthermore the transformer flux patterns were calculated and plotted to ensure the integrity of the interconnections of the multitudes of transformer wound coils.
As the mechanically adjusted rotor winding had failed, this too had to be rebuilt with more modern insulation materials being used extending the life of the winding.
A further challenge was met in the conductor required to repair the stator. The original manufactured conductor was of the braided copper type with a rectangular profile. This twisted conductor design reduced the skin effect in the current distribution and the rectangular profile ensured the optimum conductor area in the stator slot. The rectangular conductor usage was common in the 60’s and 70’s manufacturing era and had largely being discontinued by the OEM motor manufacturers. LH Marthinusen worked with their conductor supplier to successfully set up a jig to create the rectangular profile as the conductor was being braided in the manufacturing process.
After manufacture of the rectangular braided conductor, LH Marthinusen adapted one of their automated conductor covering machines for the continuous insulation covering of the rectangular conductor.
The rebuilt induction regulator was successfully tested at the LH Marthinusen works, installed and put back into operation late last year with substantial savings to the user by not having to upgrade the plant with current variable frequency drive technology.
ACTOM (Pty) Ltd is the largest manufacturer, solution provider, repairer and distributor of electro-mechanical equipment in Africa, offering a winning and balanced combination of manufacturing, service, repairs, maintenance, projects and distribution through its 40 outlets throughout Southern Africa.
ACTOM is also a major local supplier of electrical equipment, services and balance of plant to the renewable energy projects.
It also holds numerous technology, distribution and value added reseller agreements with various partners, both locally and internationally.