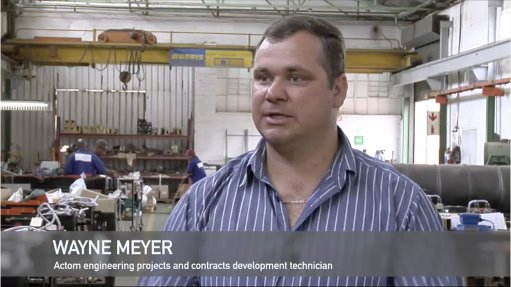
Specialised railway signalling company Actom Signalling, which locally manufactures, designs and develops railway trackside equipment and interlockings that allow for the safe movements of trains, routinely specifies the use of advanced polymer supplier Vesconite’s components in its point machines. These machines control railway tracks and switch the tracks that particular trains will be directed to.
“Actom designs and develops the machines while specialist engineering companies manufacture the components, which are then assembled into complete products, tested and delivered to our customers,” says Actom Engineering Projects and Contracts Development Technician Wayne Meyer.
Actom Signalling’s main business is railway automation, so the company produces a wide variety of products mainly for the railway industry.
Meyer says the company found minimal wear in accelerated wear testing on the Vesconite slides that are contained in its point machines when testing was carried out in November and December 2022 on a complete B1 Switchmatic Point Machine that was taken out of the production line for the express purpose of testing the performance of the point machine.
“These accelerated wear tests provide comfort to our customers on the performance of our machines and ensure the high quality of our products,” he notes. The tests were performed over a few days and put a randomly-selected machine through its expected operating life.
“The tests revealed that Vesconite slides, which are used routinely in Actom’s point machines, have an exceptionally high quality with a minimal amount of wear,” explains Meyer.
More than 5 000 movements of the point machine drive bar were tested at the company’s factory in Germiston, South Africa.
Since Vesconite slides are among the components that are used on the machines, slide wear was also tested.
Vesconite slides are located around point system detection and lock blades and drive bar at the point where they exit the point system housing.
The point system blades and bars also run on a track of Vesconite so they are enclosed within Vesconite when they are within the point system housing.
Meyer notes that most of the wear was on the bottom Vesconite slides and measured around 0.17 mm.
He says that, over the 10 year lifecycle for this product, the minimal wear is exceptional.
Wear on the top-most and side liners was almost undetectable, with wear of 0.05 mm being present, informs Meyer.
Point machines are critical in controlling the directional change of a train and for the safety of rail services.
Among the important components of the point machine are the detection blades, which determine the position of the right and left lines on the track; the locking blades, which physically locks the rail in place in a new position; and the drive slide, which is used to push the tracks into the correct position.
“With each actuation of the B1 Switchmatic point machine, the stroke of it is 300 mm, so there is 300 mm of movement over the Vesconite liner each time the machine will actuate,” describes Meyer.
“For the amount of wear, that is very good,” he says.
The B1 Switchmatic is Actom’s most popular point system, and is a well-tested machine that was first developed in the 1980s. It is the model on which Actom’s other point systems are based.
All of the machines use Vesconite extensively, with some of the original machines still operating 40 or 50 years later with low-friction low-maintenance wear-resistant Vesconite still installed.
Meyer says the company uses Vesconite slides because of their exceptional wear properties, their self-lubricating properties as well as the reduction in maintenance periods.
“There are multiple benefits to using Vesconite in our products,” he declares.
“Vesconite features mainly in the same roles throughout all of our machines. And because of the wear of the machine, anywhere where we have a friction surface, we use Vesconite in our product.”
“We have a great track record using Vesconite in our products and we'll continue using the product throughout,” Meyer asserts.
Vesconite Bearings Development Engineer and Consultant Ronnie Mugisha states that the story of Vesconite started back in 1968, when Founder and Chemical Engineer Alain Leger was researching polymer bearing materials to use in the ultra-deep gold mines of South Africa. Gold mines are harsh environments comprising extreme wetness and dirt. Now, Vesconite Bearings is a world-leading manufacturer of low-friction, low-wear polymer bearing materials for a wide range of industries.
The Vesconite factory, based in Virginia, South Africa, spans an area of 20 000 m2 and boasts advanced facilities featuring a number of processing and machining plants, as well as a chemical laboratory.
“The factory includes extrusion and injection moulding facilities, as well as 90 CNC machines that can machine from three axis to five axis. We are able to machine any shape and size of machine part up to two-metres in diameter, according to customer requirements,” states Mugisha.
Vesconite is a unique material that is self-lubricating, it is virtually maintenance free, it has a long life with very low friction and wear properties and it is easy to install.