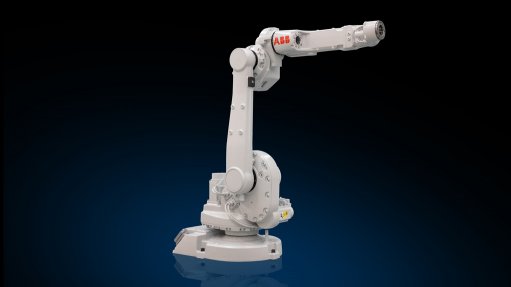
LATEST OFFERING The IRB 1660ID has a reach of 1.55 m and can handle payloads of up to 6 kg
ABB Robotics has launched its latest robot – the IRB 1660ID – for applications such as arc welding, machine tending and materials handling, which require work in tight spaces.
The new robot’s Integrated DressPack solution makes it easier to programme and simulate predictable cable movements, creates a more compact footprint and reduces maintenance costs by 50%, owing to reduced wear and tear on cables.
“Our aim . . . was to deliver a robot that offers superior and consistent quality in arc welding, as well as a fast, agile and reliable machine-tending solution,” ABB Robotics global product management head Dr Hui Zhang explained in a press statement last month.
The robot will also enable customers to increase productivity, deliver better workpiece quality and reduce cycle times, he noted.
The IRB 1660ID, with the aid of RobotStudio, ABB’s offline robot software programming tool, enables programmers to envision high-density cells, with several robots welding close to one another.
Additionally, the compact and hollow IP67 wrist enables fast and reliable movements, while the risk of collision in confined spaces is also eliminated. The combined working range of 1 390° for axes 4, 5 and 6 ensures agility inside computer numerically controlled machines.
“As a direct result of close collaboration with our customers, the IRB 1660ID also includes a new generation of accurate, efficient and reliable motors,” said Zhang.
The IRB 1660ID has a reach of 1.55 m and can handle payloads of up to 6 kg.
While the robot’s predecessor, the IRB 1600ID is installed at several sites across South Africa, ABB South Africa expects to service the first orders for the new robot in the near future.
ABB South Africa service manager Alok Maharaj told Engineering News that there was significant demand for welding, assembly, painting and finishing in the automotive and metal fabrication industries, as well as picking, packing and palletising in the pharmaceuticals and food and beverage industries.
“Traditionally, the automotive sector has driven the technology and adoption of robotics in industry. However, small to medium-sized enterprises are also starting to invest as decreasing prices and increased labour issues become a reality,” Maharaj said.