Unique precast-concrete reservoir for City of Ekurhuleni Metropolitan Municipality
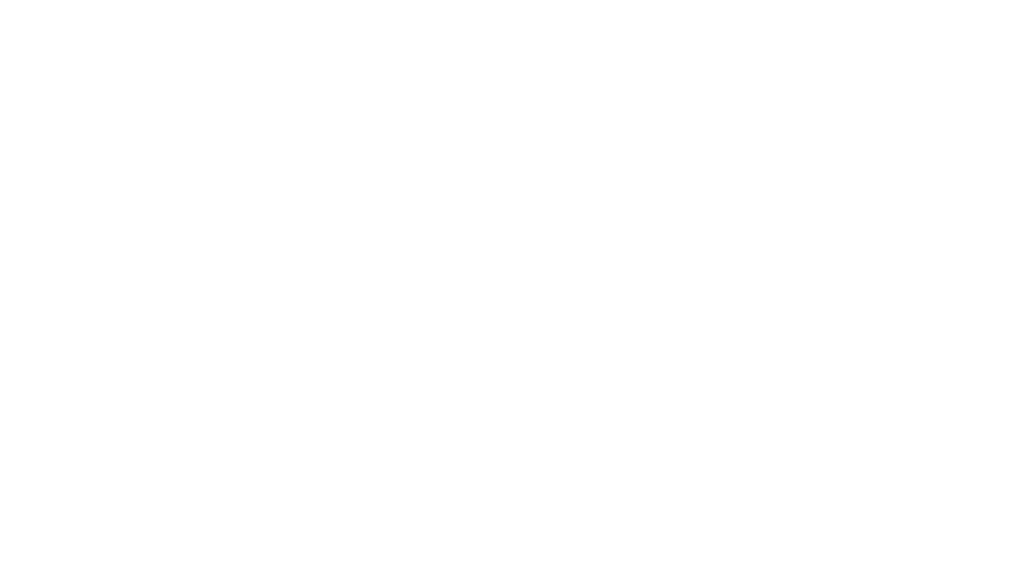
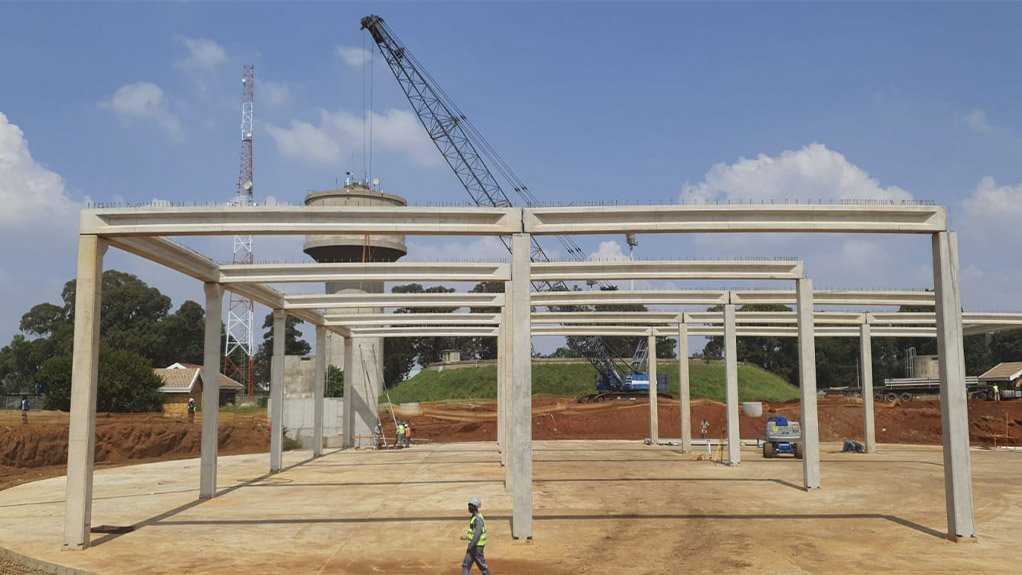
By harnessing precast-concrete technology, the various trades are able to work simultaneously to save in construction time
This article has been supplied as a media statement and is not written by Creamer Media. It may be available only for a limited time on this website.
A unique approach has been deployed to construct a new 25ML reservoir in Pam Brink, a suburb of Springs, Gauteng. With construction now nearing completion, this local innovation has again proved to be a quicker means of building large reservoirs while also providing a higher quality final structure than is possible using traditional construction methods. These are the principal reasons for the Department of Water and Sanitation of City of Ekurhuleni Metropolitan Municipality once more opting to build a reservoir in its jurisdiction using precast-concrete technology. Notably, this is the fourth large reservoir to be constructed in the City of Ekurhuleni Metropolitan Municipality in this manner.
The four reservoirs will help the City of Ekurhuleni Metropolitan Municipality augment water supply in its jurisdiction. This reservoir will cater specifically to the anticipated doubling in demand for water demand as a result of several planned new large developments in Pam Brink and Dal Fouche, a neighbouring suburb. Work on these developments will commence shortly after the finalisation of the construction of the reservoir and related infrastructure.
The system was approved by Tango’s Consultants, which was appointed as the design engineer for the construction of the reservoir and to supervise the works programme.
With more than a decade of experience in precast-concrete technology and municipal services delivery infrastructure, Infinite Consulting Engineers played a critical role in the design of the system. As an extension of the principal engineering consultant’s office on this project, Infinite Consulting Engineers also provides professional project input. This is in addition to collaborating with Tango’s Consultants to ensure that the various aspects of the work scope integrate seamlessly so as to avoid delays. Infinite Consulting Engineers also approves and accepts liability for the final precast concrete structure.
These skills and experiences are being complemented by those of Corestruc, which brings to the project extensive concrete design and application, as well as significant rigging and erection expertise and capabilities.
The roof and walls were erected in as little as three months after the cast in-situ floor, as well as the bases for the precast-concrete roof structure and ring-foundation for the prefabricated wall were completed by the principal contractor, Anita Building. Anita Building was also tasked with the earthworks and site terracing, as well as the construction of the inlet and outlet chambers and all inter-related pipe work. Moreover, the company was responsible for training a large group of sub-contractors and locals from poor communities located within the project footprint to work on less onerous aspects of the works programme. Up to 30% of the contract value has been set aside to socio-economic development.
By harnessing precast-concrete technology, the various trades are able to work simultaneously to save in construction time. Using conventional methods, work would first commence with the construction of the concrete floor slab and then the walls. The most complex and time-consuming aspect of the build, namely the reservoir roof, would be left as one of the last items in the construction programme, with work on its supporting columns only commencing once the wall had reached a predetermined height.
An approved manufacturer produces the various precast concrete elements during the earthworks and construction of the floor on behalf of Corestruc. On this project, Corestruc worked with Coreslab, which was also the approved manufacturer of the precast concrete systems that were used to build the other three reservoirs for the Department of Water and Sanitation of City of Ekurhuleni Metropolitan Municipality.
The factory is the heart of the project and extensive innovation has been implemented to ensure both efficiency of the production process and quality of the various precast-concrete elements that make up the reservoir system. For example, self-compacting concrete is used to manufacture elements that contain significant reinforcing and where conventional vibrating pokers cannot be used effectively. Trial mixes were again prepared and tested for strength and durability, while also taking into consideration the workability of the concrete. Working in a controlled environment, Coreslab is also able to ensure the perfect dosages of admixtures. This is to avoid overdosing that may delay early strength development, imperative for uninterrupted production. Another significant focus in the factory is to maintain the perfect water-to-cement ratio to ensure concrete strength. Aggregates from suitable suppliers are also graded appropriately to avoid early concrete shrinkage.
The prefabricated elements are inspected and approved for dispatch to ensure the accuracy of the placement of the cast-in components. Reinforcement bar size and placement are also verified as part of the quality control procedures at the factory.
These steps are complemented by the checks and balances introduced by Corestruc ahead of mobilising to site to commence erecting the structure. Corestruc manages the setting out and installation of the column anchors for the precast concrete roof. By confirming the dimensional accuracies before erection, the company ensures that the beams of the roof structure fit the first-time round. The precast-concrete wall panels are placed and positioned in a similar manner with the assistance of permanent locating plates that are fixed to the ring foundation.
Pam Brink reservoir has an inside diameter of 65,2m and water height of 7,8m. The roof column grids for the roof slab and beam span are 10,87m x 10,87m.
The roof structure consists of hollowcore slabs that are placed on precast-concrete beams, which are supported by the prefabricated columns. They are connected to the in-situ bases by components that are cast into the precast-concrete columns, also referred to as “column shoes”. Similar to the construction of a conventional steel structure, the precast-concrete columns are connected to hold-down bolts in the base. Suspended precast-concrete beams are then installed onto the columns. They are secured with dowels that protrude from the columns. The hollowcore slabs are then installed onto the beams and secured into place. This is achieved by tying the steel reinforcing and placing in-situ concrete into the cores of the prefabricated slabs. Stirrups protruding from the precast-concrete beam act as a mechanical interlock to form a composite mechanism with infill concrete.
The circular wall comprises 170mm-thick precast concrete panels that have been prestressed vertically. They feature 32mm-diameter polyvinyl chloride sleeves that have been positioned according to the post-tensioning design.
The panels are placed into position and then supported by push-pull props and steel brackets at the top of each. Unbonded cables are then pushed through the sleeves which are then grouted monolithically with the joints of the panels.
The grout is poured continuously in between the wall panels and horizontal cable sleeves. It is important to achieve a high strength, high flow grout with an extended pot-life and that is free of segregation. To achieve this, the water-to-cement ratio of 0:37 is manipulated with the use of admixtures and the water temperature reduced and controlled to act as a chiller in the mix. Furthermore, only cement is used in the grout mix, which also contains an un-hydrated cement that reacts with water and seals possible leaks.
After the grout has cured to a strength of 80MPa, the cables are stressed to 75% via six precast concrete buttress panels that have been spaced along the perimeter of the reservoir.
The wall is then pinned by casting a 200mm to 250mm-high reinforced kicker on the wall footing on both sides of each panel. Joints between the panels are grouted with a high-flow, high-strength grout and post-tensioning renders them in compression to achieve water tightness.
Notably, unlike most conventional post-tensioned reservoir walls which are designed to slide, Infinite Consulting Engineers and Corestruc use a “slide-and-pinned” system. Post-tensioning is undertaken when the wall is not yet fixed to the ring footing and it is, therefore, allowed to slide on a steel bearing or locating plates. The coated post-tensioned cables are not bonded to the grout with the reservoir designed to maintain a residual compression of a minimum of 1MPa in all directions. Horizontal reactions to the wall base are transferred to the ring foundation through the second phase cast in-situ kicker. This is where the ring tension in the base is also activated to resist the reaction. Additional post-tensioning of the lower part of the wall reduces the amount of rebar required in the cast in-situ ring footing.
However, the project was not without its share of challenges.
Initially, the municipality was going to build this reservoir using conventional methods. Based on the success that Infinite Consulting Engineers and Corestruc achieved on the other three reservoirs, the client body decided to also build this water-retaining structure in the same manner. Tango’s Consultants, therefore, initially designed an integrated column base-to-floor connection. Infinite Consulting Engineers and Corestruc decided to adopt the system because the principal contractor had already procured the floor and base rebar. The original grid spacings were, therefore, modified to suit Corestruc’s optimised grid proposal and the rebar cages merely relocated without the need to alter the rebar details. An advantage of this method is that it eliminates the need for waterproofing bandage along the perimeter of the base. However, it does not allow for the floor to be cast below the completed precast-concrete roof structure. As such, the curing of the floor concrete on this project required meticulous attention to detail. Conventionally, the column foundations are independent of the floor slab and feature waterproofed expansion joints around the base. This allows the bases to be constructed and roof structure to be erected before the floor slab is cast. It creates the best curing conditions, eliminating any risk of shrinkage cracks. The foundation design requires a minimum safe bearing capacity of 200kPa at founding level.
Moreover, the cast in-situ ring footing had to be modified to accommodate the larger 750mm-diameter outlet pipe sections that were also ordered by Anita Building before Corestruc was appointed to construct the reservoir using the precast-concrete system. This meant that the pipe would clash with the underside of the ring foundation. Infinite Consulting Engineers had to, thus, widen the ring foundation over the pipe to maintain a constant concrete and rebar area along the perimeter. The length of the widening was calculated to maintain sufficient transfer stress with the longitudinal rebar without creating concentrated stresses.
There are also other important advantages offered by the system that have been noted by the municipality on these projects. This includes the precast-concrete reservoirs’ smaller carbon footprint. The vertically stressed precast-concrete wall panels are thinner reducing the amount of aggregate and concrete used to build the reservoir. The hollowcore slabs, alone, reduce the carbon footprint of the structure by up to 40%, which is augmented by the use of prestressed 665mm x 460mm I-shaped beams. The self-compacting concrete used to manufacture the various precast-concrete elements also reduces the volume of the construction material required and conserves energy by eliminating the need for vibration.
It is also provides a safer means of constructing reservoirs. This is considering that the various elements are manufactured at ground level and erected on site by a skilled and experienced team.
Certainly, one of the project milestones was witnessing all the precast-concrete elements fitting into place and integrating without any discrepancies to complete a structure that is now receiving and retaining water.
Comments
Announcements
What's On
Subscribe to improve your user experience...
Option 1 (equivalent of R125 a month):
Receive a weekly copy of Creamer Media's Engineering News & Mining Weekly magazine
(print copy for those in South Africa and e-magazine for those outside of South Africa)
Receive daily email newsletters
Access to full search results
Access archive of magazine back copies
Access to Projects in Progress
Access to ONE Research Report of your choice in PDF format
Option 2 (equivalent of R375 a month):
All benefits from Option 1
PLUS
Access to Creamer Media's Research Channel Africa for ALL Research Reports, in PDF format, on various industrial and mining sectors
including Electricity; Water; Energy Transition; Hydrogen; Roads, Rail and Ports; Coal; Gold; Platinum; Battery Metals; etc.
Already a subscriber?
Forgotten your password?
Receive weekly copy of Creamer Media's Engineering News & Mining Weekly magazine (print copy for those in South Africa and e-magazine for those outside of South Africa)
➕
Recieve daily email newsletters
➕
Access to full search results
➕
Access archive of magazine back copies
➕
Access to Projects in Progress
➕
Access to ONE Research Report of your choice in PDF format
RESEARCH CHANNEL AFRICA
R4500 (equivalent of R375 a month)
SUBSCRIBEAll benefits from Option 1
➕
Access to Creamer Media's Research Channel Africa for ALL Research Reports on various industrial and mining sectors, in PDF format, including on:
Electricity
➕
Water
➕
Energy Transition
➕
Hydrogen
➕
Roads, Rail and Ports
➕
Coal
➕
Gold
➕
Platinum
➕
Battery Metals
➕
etc.
Receive all benefits from Option 1 or Option 2 delivered to numerous people at your company
➕
Multiple User names and Passwords for simultaneous log-ins
➕
Intranet integration access to all in your organisation