New electrochemical PGMs demand on way, iridium scarcity fears eased still further
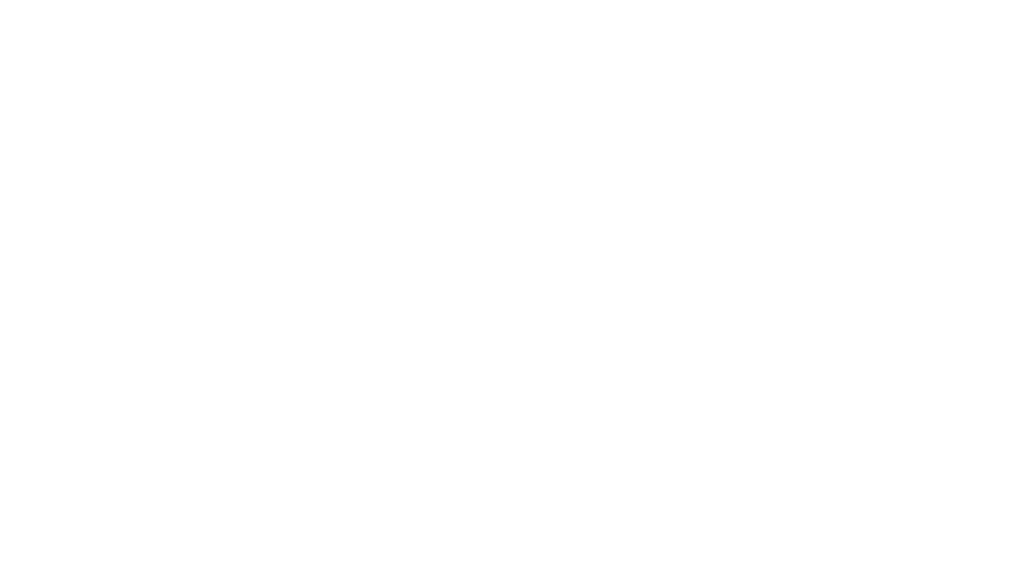
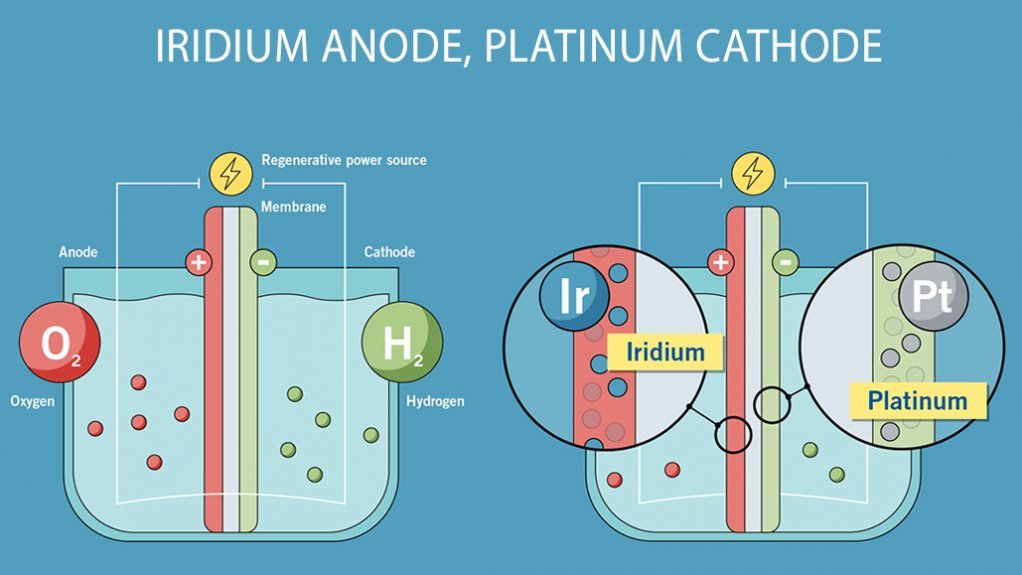
Mattiq's Dr Mike Ashley interviewed by Mining Weekly's Martin Creamer. Video: Darlene Creamer.
Iridium anode, platinum cathode of PEM fuel cell – Heraeus infographic.
JOHANNESBURG (miningweekly.com) – A far-reaching new drive is under way to ease iridium scarcity still further and, especially in the short term, demand for platinum group metals (PGMs) from electrochemical processes is on the way.
That is the news from clean chemistry company Mattiq, which aims to decarbonise chemicals production.
The Chicago-based Mattiq is intent on providing low-iridium materials for PGMs-based proton exchange membrane (PEM) electrolysers that generate green hydrogen, the globally recognised enabler of the climate-vital transition to sustainable energy and net zero emission.
“When I say low iridium, we’re typically talking about say one-third or less iridium by mass,” Mattiq product management head Dr Mike Ashley outlined to Mining Weekly in a Zoom interview. (Also watch attached Creamer Media video.)
With the aim of making low-iridium materials commercially available in 2025, Mattiq intends to clinch a partnership with a catalyst manufacturing concern in the second or third quarter of this year.
“Especially in the short term, we're going to see a pretty significant increase in demand for PGMs from electrochemical processes,” said Ashley.
Mattiq is developing electrochemical processes that run on clean electricity to decarbonise chemicals production.
“For the same reasons that iridium is quite durable over long periods of time in PEM electrolyser applications, other PGMs such as platinum, palladium, rhodium, exhibit similar characteristics where they're active and efficient catalysts, and they're very durable over long periods of time. Fortunately, all those materials are less expensive and not as scarce as iridium,” said Ashley.
Regarding the softening of PGMs demand from catalytic converters for internal combustion engine vehicles, he said: "We see electrochemistry as a potentially very important substitute demand source for PGMs moving forward.”
In addition to green hydrogen, Mattiq foresees making many more chemical products in a low-carbon way using electrocatalytic processes.
Examples of those chemical products the company sees as being attractive include acetic acid for food and beverage production, adipic acid for nylon production in particular, as well as ethylene glycol, a chemical used in coolant and antifreeze.
“These are a few examples of chemicals that are fairly carbon intensive today, that we can help to decarbonise by running through electrochemical processes that are run on clean power,” Ashley explained.
Mattiq finds that even having small quantities of PGMs in the system can improve durability considerably.
“The addition of small quantities of PGMs will always improve the durability of your system in a meaningful way.
“We think that the chemical sector is going to be the hardest-to-abate sector of the economy, due to its inherent ties to fossil fuels, leveraging both fossil fuel feedstocks and fossil fuels to run chemical processes, and we think that electrochemistry is a very key part of the decarbonisation strategy of chemical companies across the globe.
“We think that electrochemical systems are a very important piece of the puzzle to decarbonisation targets for the major chemical companies across the globe.
“We think electrochemistry uniquely allows you to bypass some of the heaviest emitting parts of chemical processing.
“Think things like high temperature process heat, compressors to produce high pressure reaction systems, we can completely circumvent these parts of the process by using electrochemical processes.
“Simply by running these systems on electricity rather than fossil fuel burners will allow chemical companies to achieve their decarbonisation targets in the coming decades,” Ashley emphasised.
BIG IRIDIUM FOCUS
Highly corrosion-resistant, iridium is the only known material that can last for long periods of operation under harsh acidic and oxidative conditions, which is why it is a key PEM catalyst material.
Because it is extremely durable, this scarcest PGM is able to drive the splitting of water into hydrogen and oxygen.
Over the course of about six weeks in the fall of 2023, Mattiq characterised over a million novel materials – that is, combinations of metals and controlled ratios – and evaluated them for their properties in PEM electrolysers.
“And now what we've been doing is validating those materials in electrolysers, running what we call accelerated stress tests in real PEM electrolyser devices to validate which of those materials we anticipate will perform well in real world operation.
“We've been running some of these experiments in partnership with all the major catalyst manufacturers and validating and qualifying these new materials with dramatically reduced iridium content and driving them towards commercialisation.
“When I say low iridium, we’re typically talking about say one-third or less by mass, so 33% or less by mass is when we start to get excited,” said Ashley.
As PEM electrolysers start to scale, Mattiq foresees that not every electrolyser manufacturer will be able to secure the volume of iridium needed to produce the number of PEM electrolysers targeted.
Quick back-of-the-envelope calculations show that about 400 kg of iridium is needed to make a gigawatt of PEM electrolysers, amid the global production of iridium set to be about 7.5 t a year.
The challenge arises because by 2030, current forecasts estimate that close to 10 GW of PEM electrolysers will be deployed a year.
Moreover, iridium is also needed for other electrochemical processes including electroplating and electrowinning, high-performance spark plugs, crucibles for recrystallisation of semiconductors at high temperatures, and electrodes for the production of chlorine in the chloralkaline process.
With demand for iridium for those other applications remaining, all supply chain constraints need to be addressed.
This arises amid the United Nation’s Green Hydrogen Catapult initiative committing to secured financing by 2026 and targeted commissioning in 2027 of 45 GW of electrolyser activity.
PEM electrolysers, with iridium anodes and platinum cathodes, are the leading technology for synthesising zero-carbon hydrogen fuel using renewable energy.
They provide the solution to the decarbonisation of heavy industry sectors and will constitute up to 25% of total final energy use in a net-zero economy.
There is heavy dependence on PEM electrolysis technology because of it being able to cope best with renewable energy fluctuations.
In addition, platinum, iridium and now also ruthenium, play electrocatalytic roles in splitting water into hydrogen and oxygen, with PGMs also being used as catalysts to crack ammonia into nitrogen and hydrogen and convert carbon dioxide into methanol or other hydrogen-carrier molecules.
The essential need to have enough iridium available to accommodate and accompany PEM electrolysis growth is also being met by highly successful thrifting achievements as well as through the addition of ruthenium by particularly Heraeus Precious Metals of Germany.
Thrifting not only reduces reliance on iridium but also reduces material cost. Primary production of ruthenium, also a PGM, is three-and-a-half times greater than the primary production of iridium.
While some are seeking to substitute PGMs completely, being able to do so effectively is seen as highly unlikely by chemist Dr Philipp Walter, Heraeus’ new business development executive VP.
Comments
Press Office
Announcements
What's On
Subscribe to improve your user experience...
Option 1 (equivalent of R125 a month):
Receive a weekly copy of Creamer Media's Engineering News & Mining Weekly magazine
(print copy for those in South Africa and e-magazine for those outside of South Africa)
Receive daily email newsletters
Access to full search results
Access archive of magazine back copies
Access to Projects in Progress
Access to ONE Research Report of your choice in PDF format
Option 2 (equivalent of R375 a month):
All benefits from Option 1
PLUS
Access to Creamer Media's Research Channel Africa for ALL Research Reports, in PDF format, on various industrial and mining sectors
including Electricity; Water; Energy Transition; Hydrogen; Roads, Rail and Ports; Coal; Gold; Platinum; Battery Metals; etc.
Already a subscriber?
Forgotten your password?
Receive weekly copy of Creamer Media's Engineering News & Mining Weekly magazine (print copy for those in South Africa and e-magazine for those outside of South Africa)
➕
Recieve daily email newsletters
➕
Access to full search results
➕
Access archive of magazine back copies
➕
Access to Projects in Progress
➕
Access to ONE Research Report of your choice in PDF format
RESEARCH CHANNEL AFRICA
R4500 (equivalent of R375 a month)
SUBSCRIBEAll benefits from Option 1
➕
Access to Creamer Media's Research Channel Africa for ALL Research Reports on various industrial and mining sectors, in PDF format, including on:
Electricity
➕
Water
➕
Energy Transition
➕
Hydrogen
➕
Roads, Rail and Ports
➕
Coal
➕
Gold
➕
Platinum
➕
Battery Metals
➕
etc.
Receive all benefits from Option 1 or Option 2 delivered to numerous people at your company
➕
Multiple User names and Passwords for simultaneous log-ins
➕
Intranet integration access to all in your organisation