Coal waste repurposing
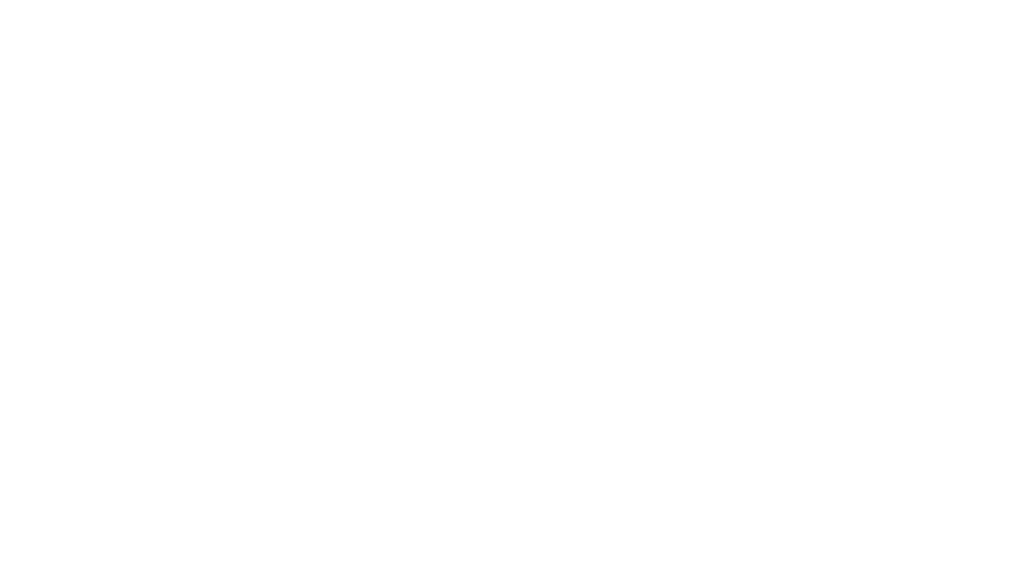
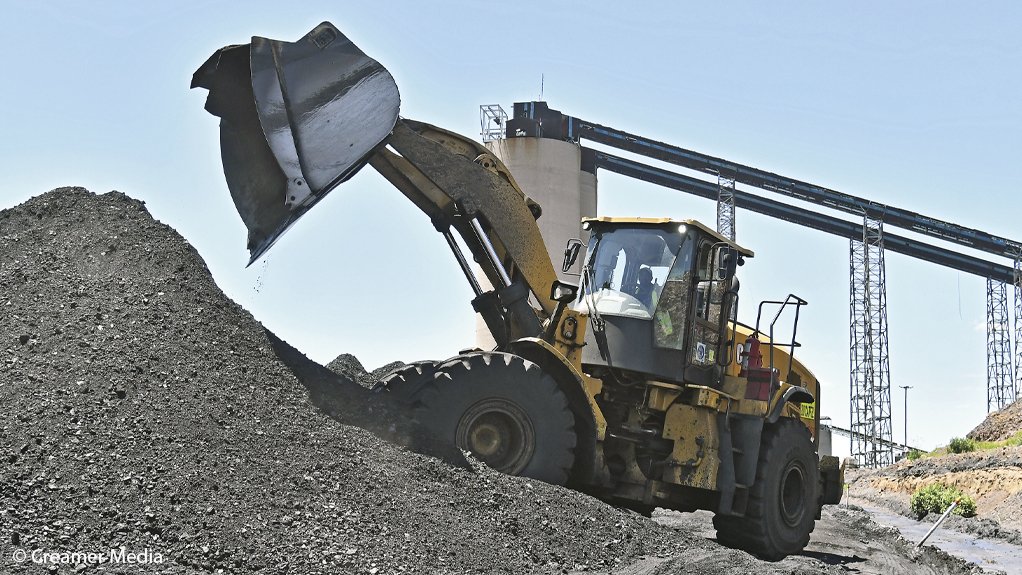
REHABILITATING STOCKPILES The ability to impact positively on stockpiles and product offers a compelling opportunity to coal producers
Photo by Creamer Media's Donna Slater
An opportunity exists for the target rehabilitation of coarse and ultrafine coal waste streams and stockpiles in the local coal sector, said green coal solutions provider River Energy South Africa (Resa) GM Dale Mclean.
The technique can be achieved through decreasing coal beneficiation process waste and increasing yield from every tonne of coal mined.
Speaking at the Southern African Coal Processing Society’s International Coal Conference in Secunda on August 16, Mclean added that Resa has targeted the rehabilitation of ultrafine coal waste streams and stockpiles to decrease the waste going into tailings dams and filter processes, as well as associated waste that is reticulated into final discards.
As such, the end-product produced through Resa’s technology contains lower embedded emissions and a smaller net environmental footprint than that of primary run-of-mine (RoM) coal.
From coal exploration to the end-user, waste stockpiles are produced, which need to be rehabilitated: “We try to intercept the waste and reclaim it from the stockpiles present. It's easier to intercept the waste than it is to reclaim it from a dam.”
This helps coal processers to prevent waste from going into stockpiles and in recovering saleable material from waste piles, added Mclean.
Resa’s technology offers two solutions to reduce the rehabilitation liabilities of their users: ultrafine coal benefication and binderless coal briquetting (BCB), the former being employed to yield more coal from every tonne of RoM coal, resulting in decreased waste fines or filter cake being produced during the beneficiation of coal.
Coal briquetting technology serves to upgrade low-value or waste coal using a low-cost process of dehydration and compaction.
This rehabilitation can increase revenue, in addition to reducing costs for coal producers, reduce material requirement for tailings facilities, as well as water and air pollution. Capital expenditure and operational expenditure are also lower, owing to the eradication of wet slimes and fewer tailings facilities and liabilities.
Mclean noted that the local coal value chain has become static, and that this rehabilitation method can help to boost the value chain by creating value from ultrafine coal.
“Our primary focus is on BCB without any kind of additive or foreign substance,” he said.
“We've built a framework using international best practice. The coal industry can prove some of these positive environmental impacts we're achieving, including fewer tailings facilities, quicker return of water, and lowering emissions such as sulphur.”
While supporting sustainable practices, this rehabilitation method can also contribute to supporting jobs in the coal industry, he added.
Ultrafine Coal Beneficiation, bcb
Mclean emphasised the importance of an integrated circuit in the beneficiation of ultrafine coal products, and that different technologies for coal beneficiation are suited to different mining operations.
“We look at what is appropriate for different circumstances. It would start with a coarse coal reclamation plant – such as a typical dense-media separation plant – followed by ultrafine coal beneficiation.
“If you’re getting below 20 cadmium in your coal ash with arising fines, stored fines and fracture, it’s going to be difficult to create value output. This requires beneficiation,” he explained.
Ultrafine coal recovery plants are designed to intercept waste slurry arising from the coal processing activities using circuits with a low operational cost.
“Different beneficiation technologies depend on what the final product is that you can produce,” said Mclean, who added that upgraded material becomes a saleable product.
However, he noted that there is a maximum volume of such product that can be sent to carbonised-fuel users who have covered stockpiles, owing to the coal being fine and, consequently, negatively affected by wind or rain.
“One needs to treat it carefully, and there’s a maximum limit for demand. Therefore, after this process one would need to agglomerate.”
The technology has achieved positive results from combustion and materials handling tests obtained on South African coals.
“We focus on coal briquetting, as we try to keep things simple and cost effective. The value chain around finding coal binder and bringing that to site to homogenously blend with coal fines is a challenge. We avoid that through a simple process of dehydration and compaction.”
Mclean stressed that the ability to impact positively on stockpiles and product sets – currently produced through ultrafine upgraded coal and as coal briquettes – offers “a compelling opportunity” to coal producers.
“This allows you to minimise the use of additional primary rock. You’re also able to produce a product from waste that’s been premined. In this lies savings from an environmental perspective, and latent resources are waiting to be produced.”
He concuded that such coal stocks are already above ground and easier to access, resulting in the processing of such stocks impacting positively on net environmental footprints.
Comments
Press Office
Announcements
What's On
Subscribe to improve your user experience...
Option 1 (equivalent of R125 a month):
Receive a weekly copy of Creamer Media's Engineering News & Mining Weekly magazine
(print copy for those in South Africa and e-magazine for those outside of South Africa)
Receive daily email newsletters
Access to full search results
Access archive of magazine back copies
Access to Projects in Progress
Access to ONE Research Report of your choice in PDF format
Option 2 (equivalent of R375 a month):
All benefits from Option 1
PLUS
Access to Creamer Media's Research Channel Africa for ALL Research Reports, in PDF format, on various industrial and mining sectors
including Electricity; Water; Energy Transition; Hydrogen; Roads, Rail and Ports; Coal; Gold; Platinum; Battery Metals; etc.
Already a subscriber?
Forgotten your password?
Receive weekly copy of Creamer Media's Engineering News & Mining Weekly magazine (print copy for those in South Africa and e-magazine for those outside of South Africa)
➕
Recieve daily email newsletters
➕
Access to full search results
➕
Access archive of magazine back copies
➕
Access to Projects in Progress
➕
Access to ONE Research Report of your choice in PDF format
RESEARCH CHANNEL AFRICA
R4500 (equivalent of R375 a month)
SUBSCRIBEAll benefits from Option 1
➕
Access to Creamer Media's Research Channel Africa for ALL Research Reports on various industrial and mining sectors, in PDF format, including on:
Electricity
➕
Water
➕
Energy Transition
➕
Hydrogen
➕
Roads, Rail and Ports
➕
Coal
➕
Gold
➕
Platinum
➕
Battery Metals
➕
etc.
Receive all benefits from Option 1 or Option 2 delivered to numerous people at your company
➕
Multiple User names and Passwords for simultaneous log-ins
➕
Intranet integration access to all in your organisation