Ford Motor Company investment project, South Africa – update
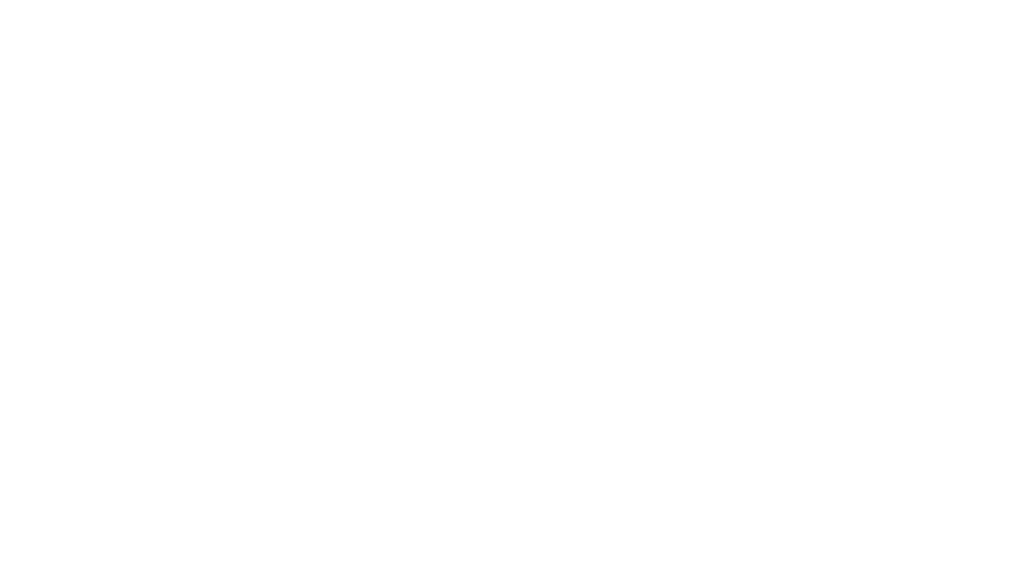
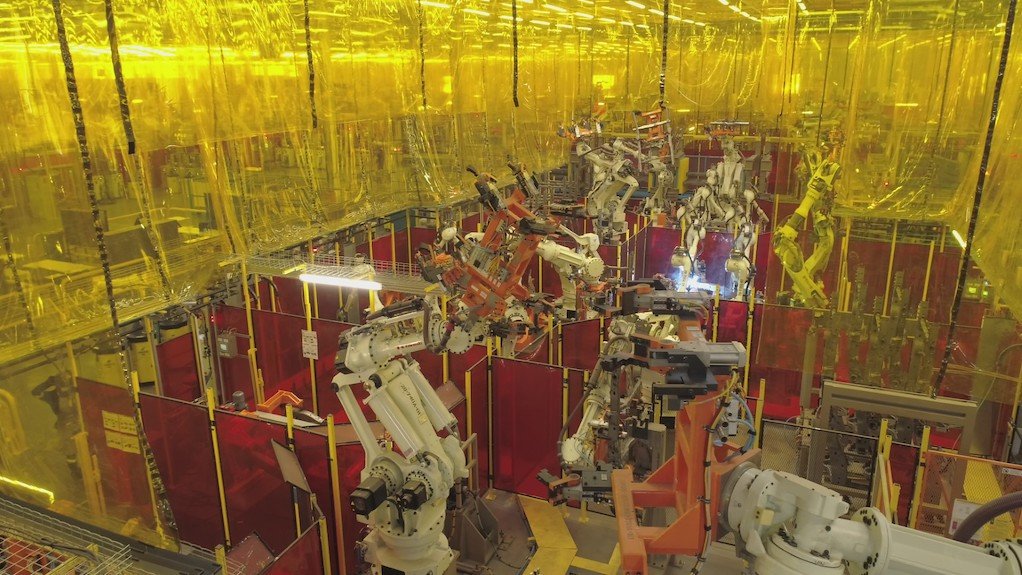
Photo by Ford Motor Company Southern Africa
Name of the Project
Ford Motor Company investment project.
Location
Pretoria, in Gauteng, South Africa.
Project Owner/s
Ford Motor Company, through its Ford Motor Company Southern Africa (FMCSA) subsidiary.
Project Description
Ford Motor Company is undertaking the biggest investment in its 97-year history in South Africa. The project is also one of the biggest-ever investments in the South African automotive industry.
The investment will increase the capacity at the Silverton plant from 168 000 to 200 000 vehicles a year, supporting the production of the new Ford Ranger pickup truck for the domestic market and exports to more than 100 global markets. The plant will also manufacture Volkswagen (VW) pickup trucks as part of the Ford-VW strategic alliance.
The project will entail extensive upgrades to the Silverton plant, which will increase production volume and drive significant improvements in production efficiency and vehicle quality. These include the construction of a new body shop with the latest robotic technology, and a new high-tech stamping plant, both of which will be located on site for the first time.
The plant will use a high-speed line to produce all the major sheet metal components for the new Ranger. It includes a fully automated storage and retrieval system for stamping dies, which will be housed in the roof of the facility, thus eliminating related labour-intensive processes. In addition, a modern blue-light scanner system, which scans surfaces for imperfections, will ensure that the highest-quality final product leaves the stamping plant.
Extensive upgrades will also be undertaken on the box line, paint shop and final assembly to improve vehicle flow within the plant, along with the expansion of the container and vehicle yards.
Ford will also build new-vehicle-modification and training centres – the latter will ensure that all Ford employees are equipped with the knowledge and skills required to maximise the efficiencies of the enhanced Silverton facilities.
The new investment programme builds on the recently announced Project Blue Oval renewable-energy project, which aligns with the company’s global target of using 100% locally sourced renewable energy for all its manufacturing plants by 2035, and achieving carbon neutrality by 2050.
The first phase of Project Blue Oval is under way with the construction of solar carports for 4 200 vehicles at the Silverton plant.
Potential Job Creation
The expanded production will create 1 200 incremental jobs in South Africa, increasing the local Ford workforce to 5 500 employees, and adding an estimated 10 000 new jobs across Ford’s local supplier network, bringing the total to 60 000.
Capital Expenditure
$1.05-billion (R15.8-billion – 2021).
The investment includes $686-million, or R10.3-billion (2021), for extensive upgrades to the Silverton assembly plant, which will increase production volume and drive significant improvements in production efficiency and vehicle quality. Ford will also invest $365-million (R5.5-billion – 2021) to upgrade tooling at the company’s major supplier factories.
Planned Start/End Date
Ford SA will produce the new-generation Ranger pickup at the Tshwane plant in 2022.
Latest Developments
Vehicle manufacturer Ford's new frame line, in the Tshwane Automotive Special Economic Zone, adjacent to its Silverton assembly plant, has started operations in preparation for the start of next-generation Ranger production later this year.
It is the final and biggest aspect of Ford Motor Company’s R15.8-billion investment in its South African operations.
The facility measures 100 000 m2, uses 585 robots and has more than 1 000 tools in the highly automated frame-welding and assembly process, the company has noted.
The frame line is the only Ford-owned and -operated chassis manufacturing facility in the world and boasts some of the most advanced robotic manufacturing and quality-control systems currently available.
The ladder-frame chassis of the Ranger pickup is fundamental to its overall quality, performance and durability, whether used as an everyday family vehicle or in hard-working commercial applications, Ford South Africa VP operations Ockert Berry has explained.
Rigorous quality-control measures are in place, including in-line Perceptron measurement of every chassis produced in the plant. The blue-light scanner system creates highly detailed three-dimensional models of the entire chassis or individual sections, with the results compared with a stored design specification. These ensure that there are no compromises in quality.
At the heart of the frame line are two identical lines that manufacture these large and heavy steel components, with 15 derivatives produced to support the various model iterations, as well as the local and export market requirements.
Further, 387 hourly employees and 25 salaried staff, all of whom have undergone extensive in-plant training, run the frame line in a two-shift operating pattern.
“The facility is 95% automated, relying on 585 robots to assemble and weld the frames. We use the latest SKS automated intelligent welding system with I&K Pulse technology to guarantee the highest level of precision welding and consistency,” Ford Frame Line area manager Yetheen Gengan has said.
Alongside the production area is a sophisticated multistage e-coat facility where the frames are completely immersed in a range of cleaning and phosphate solutions before being submerged in an electrically charged tank where the paint is uniformly bonded to the metal. Thereafter, a robotic station applies a protective wax inside the frame to provide rust protection and durability.
“With these advanced and extremely accurate measurement and scanning systems, we are able to track real-time data to quickly identify and address any quality issues before the frame leaves the plant. All of the data is stored in our quality management system to monitor trends, and we can access the measurements and imaging data at any point, should a concern be raised on any chassis we produced,” Gengan has explained.
As part of the extensive quality checks, the plant also incorporates a weld tear-down facility with world-class macrocutting and etching processes that assess the strength and integrity of the individual welds.
Further, once the frames are completed, they are stored in a below-ground, finished-goods area with a storage capacity for 6 000 units.
From there, the frames are processed through an automated sequencing facility and moved across to the Silverton assembly plant where the suspension and brake components, differentials, engine, gearbox, exhaust and fuel tank are fitted in subassembly areas before being mated with the cab and load box on the trim, chassis and final line.
Key Contracts, Suppliers and Consultants
None stated.
Contact Details for Project Information
FMCSA GM communications Minesh Bhagaloo, tel +27 12 842 2691 or email mbhagalo@ford.com.
Comments
Press Office
Announcements
What's On
Subscribe to improve your user experience...
Option 1 (equivalent of R125 a month):
Receive a weekly copy of Creamer Media's Engineering News & Mining Weekly magazine
(print copy for those in South Africa and e-magazine for those outside of South Africa)
Receive daily email newsletters
Access to full search results
Access archive of magazine back copies
Access to Projects in Progress
Access to ONE Research Report of your choice in PDF format
Option 2 (equivalent of R375 a month):
All benefits from Option 1
PLUS
Access to Creamer Media's Research Channel Africa for ALL Research Reports, in PDF format, on various industrial and mining sectors
including Electricity; Water; Energy Transition; Hydrogen; Roads, Rail and Ports; Coal; Gold; Platinum; Battery Metals; etc.
Already a subscriber?
Forgotten your password?
Receive weekly copy of Creamer Media's Engineering News & Mining Weekly magazine (print copy for those in South Africa and e-magazine for those outside of South Africa)
➕
Recieve daily email newsletters
➕
Access to full search results
➕
Access archive of magazine back copies
➕
Access to Projects in Progress
➕
Access to ONE Research Report of your choice in PDF format
RESEARCH CHANNEL AFRICA
R4500 (equivalent of R375 a month)
SUBSCRIBEAll benefits from Option 1
➕
Access to Creamer Media's Research Channel Africa for ALL Research Reports on various industrial and mining sectors, in PDF format, including on:
Electricity
➕
Water
➕
Energy Transition
➕
Hydrogen
➕
Roads, Rail and Ports
➕
Coal
➕
Gold
➕
Platinum
➕
Battery Metals
➕
etc.
Receive all benefits from Option 1 or Option 2 delivered to numerous people at your company
➕
Multiple User names and Passwords for simultaneous log-ins
➕
Intranet integration access to all in your organisation