Craft-Star system debuts in Africa
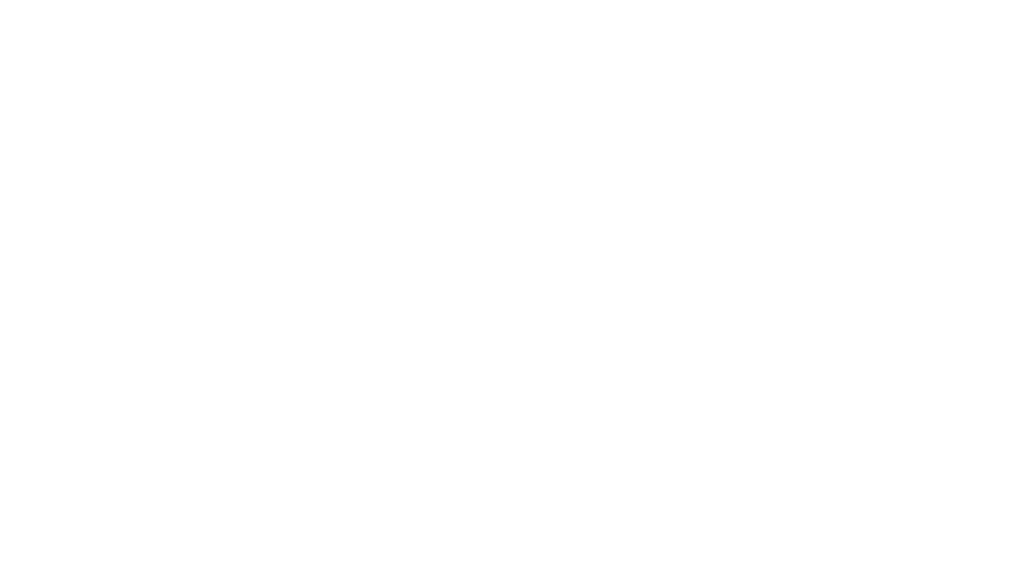
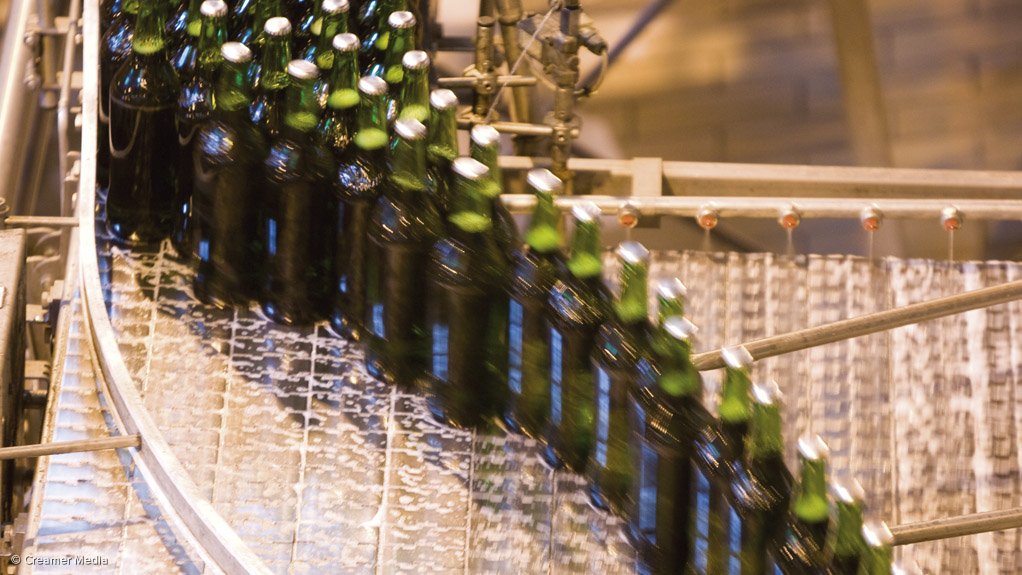
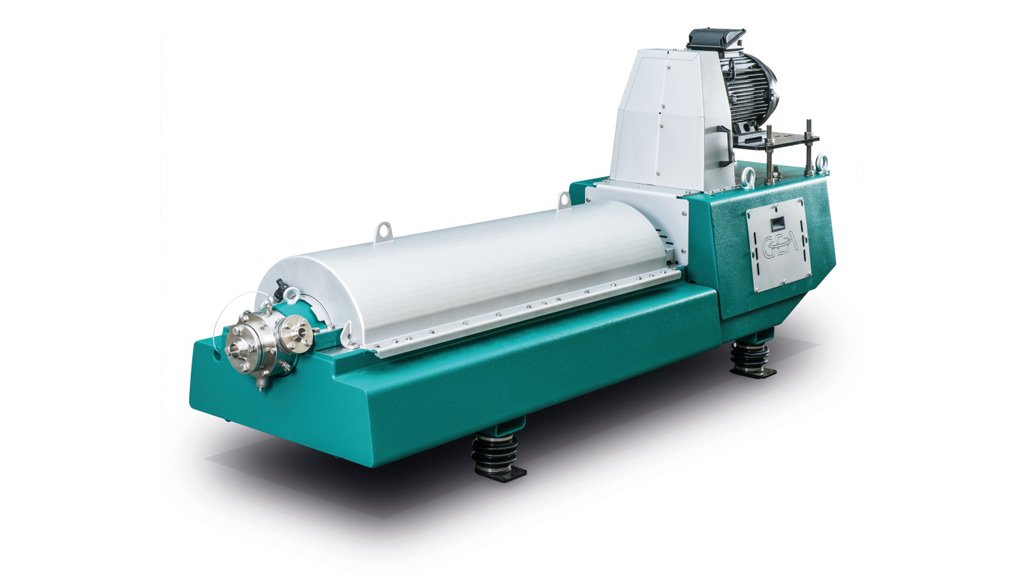
CATERING TO CRAFT BEER GEA offers solutions to craft beer breweries that meet the demand for higher production capacities with lower capital expenditure
Photo by Duane Daws
IMPROVED WINE PRODUCTION GEA’s CF 7000 decanter increases operational efficiency through its automated, continuous operation, producing higher yields of wine without compromising on quality
Food processing technology provider GEA Africa commissioned Africa’s first Craft-Star system at a craft beer brewery in South Africa, last month.
The Craft-Star, which has experienced great success in Europe and the US, is a skid-mounted brew system designed specifically for artisan craft breweries processing batch sizes of 2 500 ℓ of hot wort. GEA also offers the Compact-Star, which is suited to medium-sized breweries brewing larger batches.
GEA brewing sales engineer Ashley Sissing notes that there has been an increase in demand for craft beers in the South African market and GEA is, thus, introducing solutions specifically designed for this process.
“A key challenge facing local breweries, however, is a demand for higher production capacities with little capital expenditure available. GEA believes that this can be achieved by increasing production efficiencies and upgrading manufacturing equipment or installing new manufacturing equipment. All systems developed and installed by GEA, moreover, aim to cater to the specific application at hand.”
Sissing describes the Craft-Star as a cost-effective alternative to standard brewing systems, which does not sacrifice quality-related technological features. It is designed as an off-the-shelf system to ensure the lowest possible engineering costs for customers, and is prepiped, prewired and tested in GEA’s workshops prior to shipping so that it arrives at the site ready for installation.
She highlights that this reduces installation periods, commissioning times and related on-site costs. She further notes that the Craft-Star and Compact-Star are modular systems that can be expanded as production requirements increase.
The Craft-Star is available in a two-vessel configuration, with a mash tun/lauter tun and whirlpool/wort kettle that is ready for single-stem infusing mashing and ideally suited to ale breweries. A three-vessel configuration can also be supplied with a mash tun, lauter tun and whirlpool/wort kettle to process up to five brews a day, with the system being able to manage all infusion and decoction mashing regimes. This allows for brewing to a wide range of international beer styles.
The base frame of the Craft-Star holds pumps, valves, power cabinets and other components, which can be operated from the front side. The unit also includes stairs and railing, functioning as an operator platform.
The unit is made from stainless steel, ensuring durability and hygiene, with flange connections allowing for easy connection of the Craft-Star to media suppliers and wort coolers. The unit offers semiautomatic control through a Gearboxx system, which controls the quality processes, including mashing, lautering, wort boiling and whirlpooling.
The system also offers a touch-panel monitor, a recipe editor and database, the ability to switch between manual and automatic modes, process parameter monitoring, curve visualisation and a brew report.
Green Filtration
GEA also introduced the Clearamic filter in 2014, a beer filtration system that reduces operational costs through its elimination of kieselguhr – a soft, highly porous siliceous sedimentary rock that is often used as a filter medium in beer and wine. Sissing explains that kieselguhr is nondegradable and, thus, the elimination of it in filtration has significant environmental benefits.
“While there are other kieselguhr-free filtration systems on the market that use membrane filtration, the Clearamic system is unique in the brewing industry in its use of ceramic membranes, which have a much longer life span, compared with other membrane filters.”
Membranes are bought with the system and last the entire service life of the system, which is a minimum of ten years. In addition, using ceramic membranes results in beer filtration being carried out with greater process reliability, as there is no risk of membrane damage, thereby ensuring a permanently consistent beer quality, Sissing points out. Ceramic is also food neutral, so there is no risk of taste contamination and no expensive cleaning agents are required.
In conjunction with its product, GEA offers a range of services, including technical audits, which analyse a brewery’s existing processes to determine improvements in operational efficiencies and increase throughput.
“This can then be executed by GEA through turnkey projects to realise agreed-upon production targets. We try to work closely with breweries to develop products and processes that will be of mutual benefit,” Sissing says.
Efficient Winery Equipment
GEA also offers solutions for the winery industry, including the CF 7000 decanter and an integrated direct drive separator, which significantly increase efficiency.
GEA Africa market development engineer Jaco Coetzee says the CF 7000 decanter can increase operational efficiency through its automated, continuous operation, producing higher yields of wine without compromising on quality. He explains that, after grapes go through a destemmer, they are pumped into a holding tank, from which the decanter can be continuously fed. “This is much faster than the conventional batch process of a traditional press.”
The decanter has proved a success at its first installation in South Africa, at Waboomsrivier Winery, located between Worcester and Ceres, in the Western Cape. The decanter was installed in 2014 following the winery’s decision to expand its operations. Rather than buying extra drainers, a press, drum filter and centrifuge, Waboomsrivier Winery manager Bennie Wannenburg says the winery opted for the all-in-one decanter system.
“The decanter enables us to take the juice from the grapes directly to the fermentation tanks. With our previous system, we generally produced 550 ℓ of wine per ton of A-class juice; however, with the decanter, we are producing about 760 ℓ.”
The integrated direct drive separator helps wineries to limit possible product losses and produce more A-class product while reducing maintenance and energy costs, says Coetzee. In addition, it requires less space and offers reduced noise levels.
Comments
Announcements
What's On
Subscribe to improve your user experience...
Option 1 (equivalent of R125 a month):
Receive a weekly copy of Creamer Media's Engineering News & Mining Weekly magazine
(print copy for those in South Africa and e-magazine for those outside of South Africa)
Receive daily email newsletters
Access to full search results
Access archive of magazine back copies
Access to Projects in Progress
Access to ONE Research Report of your choice in PDF format
Option 2 (equivalent of R375 a month):
All benefits from Option 1
PLUS
Access to Creamer Media's Research Channel Africa for ALL Research Reports, in PDF format, on various industrial and mining sectors
including Electricity; Water; Energy Transition; Hydrogen; Roads, Rail and Ports; Coal; Gold; Platinum; Battery Metals; etc.
Already a subscriber?
Forgotten your password?
Receive weekly copy of Creamer Media's Engineering News & Mining Weekly magazine (print copy for those in South Africa and e-magazine for those outside of South Africa)
➕
Recieve daily email newsletters
➕
Access to full search results
➕
Access archive of magazine back copies
➕
Access to Projects in Progress
➕
Access to ONE Research Report of your choice in PDF format
RESEARCH CHANNEL AFRICA
R4500 (equivalent of R375 a month)
SUBSCRIBEAll benefits from Option 1
➕
Access to Creamer Media's Research Channel Africa for ALL Research Reports on various industrial and mining sectors, in PDF format, including on:
Electricity
➕
Water
➕
Energy Transition
➕
Hydrogen
➕
Roads, Rail and Ports
➕
Coal
➕
Gold
➕
Platinum
➕
Battery Metals
➕
etc.
Receive all benefits from Option 1 or Option 2 delivered to numerous people at your company
➕
Multiple User names and Passwords for simultaneous log-ins
➕
Intranet integration access to all in your organisation