VWSA installs automated guided vehicle line at engine plant
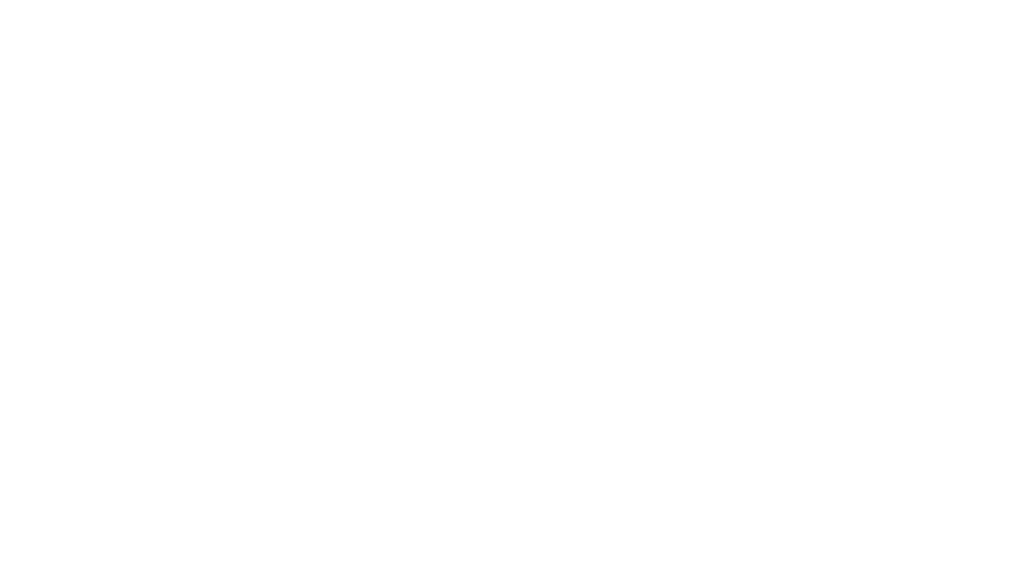

SMART MOVER What differentiates VWSA’s AGV line from other AGV lines is that it is a completely contactless system
Photo by VWSA
Volkswagen Group South Africa (VWSA) has installed an automated guided vehicle (AGV) line to replace the traditional roller conveyor used on the VW250 engine line.
An AGV is a mobile robot that follows markers or cabling in the floor, or uses vision or lasers to follow a preset route. AGVs are most often used in industrial applications to move materials around a manufacturing facility or warehouse.
The AGV line at VWSA’s Uitenhage plant, in the Eastern Cape, is located in the engine subassembly area, which is in the final assembly area.
The line delivers new-generation EA211 and EA288 engines, which are being fitted in a number of new models within the Audi, Volkswagen, Seat and Skoda ranges.
The project was priced at R13.35-million. This, however, excludes equipment such as controlling systems, bolting equipment, gearbox filling equipment and infrastructure.
The AGV vehicles were delivered by German company Daum + Partner.
Similar AGV systems have been introduced at Volkswagen plants in Wolfsburg (Germany), Chattanooga (US) and China.
What differentiates VWSA’s AGV line from other AGV lines is that it is a completely contactless system. The AGV knows exactly where to go by following induction cables hidden under the concrete floor.
Two of those cables provide enough power to drive the vehicle, so there is no direct contact with cables or tracks, explains VWSA manufacturing planning and plant engineering manager Sarel Breitenbach.
“The cables also give enough power not only to drive the system but also to lift a complete engine gearbox powertrain weighing roughly 150 kg.”
Older versions of AGVs are battery-powered, which means they need to be docked in a charging station at random intervals before being reintroduced into the production line.
The benefits the AGV project delivers are numerous, says Breitenbach.
The biggest improvement has been in the area of ergonomics. For one, there is greater accessibility to the engine and gearbox from all sides, as the powertrain is on a turntable which can rotate to suit the operator.
There is also a lifting table on top, making it possible to accommodate different operator heights – the old conveyor system often saw operators climb on steel platforms for proper reach.
The workstation has also been optimised and is now 3 m in length, as opposed to 0.8 m on the old system. This allows for better line-side supply of parts.
The roof structure on the line is also suspended, with no columns obstructing the delivery of parts, adds Breitenbach.
“It was an extremely tough task to have only three weeks to remove the old system and install the new one, and from day one to start building 348 cars a day – that was the ask, but I am proud to say we achieved it,” says Breitenbach.
Comments
Press Office
Announcements
What's On
Subscribe to improve your user experience...
Option 1 (equivalent of R125 a month):
Receive a weekly copy of Creamer Media's Engineering News & Mining Weekly magazine
(print copy for those in South Africa and e-magazine for those outside of South Africa)
Receive daily email newsletters
Access to full search results
Access archive of magazine back copies
Access to Projects in Progress
Access to ONE Research Report of your choice in PDF format
Option 2 (equivalent of R375 a month):
All benefits from Option 1
PLUS
Access to Creamer Media's Research Channel Africa for ALL Research Reports, in PDF format, on various industrial and mining sectors
including Electricity; Water; Energy Transition; Hydrogen; Roads, Rail and Ports; Coal; Gold; Platinum; Battery Metals; etc.
Already a subscriber?
Forgotten your password?
Receive weekly copy of Creamer Media's Engineering News & Mining Weekly magazine (print copy for those in South Africa and e-magazine for those outside of South Africa)
➕
Recieve daily email newsletters
➕
Access to full search results
➕
Access archive of magazine back copies
➕
Access to Projects in Progress
➕
Access to ONE Research Report of your choice in PDF format
RESEARCH CHANNEL AFRICA
R4500 (equivalent of R375 a month)
SUBSCRIBEAll benefits from Option 1
➕
Access to Creamer Media's Research Channel Africa for ALL Research Reports on various industrial and mining sectors, in PDF format, including on:
Electricity
➕
Water
➕
Energy Transition
➕
Hydrogen
➕
Roads, Rail and Ports
➕
Coal
➕
Gold
➕
Platinum
➕
Battery Metals
➕
etc.
Receive all benefits from Option 1 or Option 2 delivered to numerous people at your company
➕
Multiple User names and Passwords for simultaneous log-ins
➕
Intranet integration access to all in your organisation